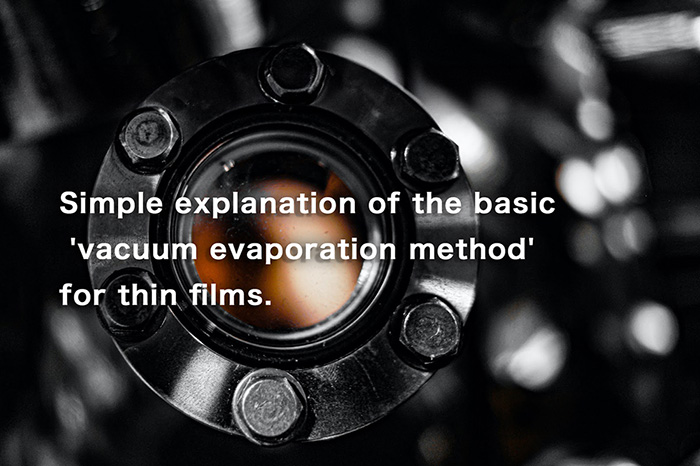
There are several types of thin film formation methods.
This article demonstrates the principles and types of one of ‘vacuum evaporation method’.
At the end of the article, the vacuum evaporation method is explained in an easy-to-understand manner using familiar examples, which we hope will be of use to you.
Contents
One of the methods to make thin film: ‘Vacuum evaporation method’.
There are several types of thin film formation methods, as shown in the diagram below.
How to make thin films | Detail |
---|---|
evaporation method | This technique forms thin films by evaporating deposition materials such as metals and oxides in a vacuumed container and depositing them on the surfaces of opposing substrates. References※1.2.3.4 |
Ion plating (IP) method | In principle, it is almost identical to the evaporation method, but the evaporation material is ionized by passing the evaporation particles through a plasma. A negative voltage is applied to the substrate to be deposited and the ionized deposition material is accelerated to impact the substrate to form a thin film. Ionization and acceleration can be used to create highly adherent films. References※1.5 |
Sputtering method | Ions (usually Ar+ ions) created in the plasma by the discharge strike a plate (target) of the deposition material, which splashes the material. This is a method whereby the flung deposition material flies to the substrate to form a thin film. The sputtering method can be used for a wide range of deposition materials, such as metals and alloys with high melting points, which are difficult to deposit with the vapor deposition method. References※1.5.6 |
Chemical vapor deposition (CVD) method | A method whereby gases containing the elements to be deposited are pumped onto the surface of a substrate and the films are deposited through chemical reactions and decomposition. There are different types of CVD, including thermal CVD, where the substrate is heated, and plasma CVD, where the reaction tube is depressurized and plasma is generated. References※1.7.8 |
Atomic layer deposition (ALD) method | Although said to be a type of CVD, atomic layer deposition (ALD) is a method in which two or more types of raw material gases (precursor, precursor) are alternately introduced and exhausted to form a film by reacting the adsorbed raw material molecules on the surface of the deposited film. references※8.9 |
References:
※1 書籍「今日からモノ知りシリーズ トコトンやさしい真空の本」 p92-p93
※2 尾池工業株式会社
※3コトバンク
※4ウィキペディア
※5東邦化研株式会社
※6尾池工業株式会社
※7ウィキペディア
※8化学的気相成長法の基本 論文
※9ウィキペディア
Here, we explain one of these methods, the ‘vacuum evaporation method’.
Vacuum evaporation is a technique whereby the material to be made into a thin film is heated and evaporated in a vacuum, the vaporized material is made solid again on the substrate and deposited as a thin film.
In vacuum evaporation, evaporated particles reach the substrate without colliding with other molecules on the way, so they do not lose or gain energy on the way.
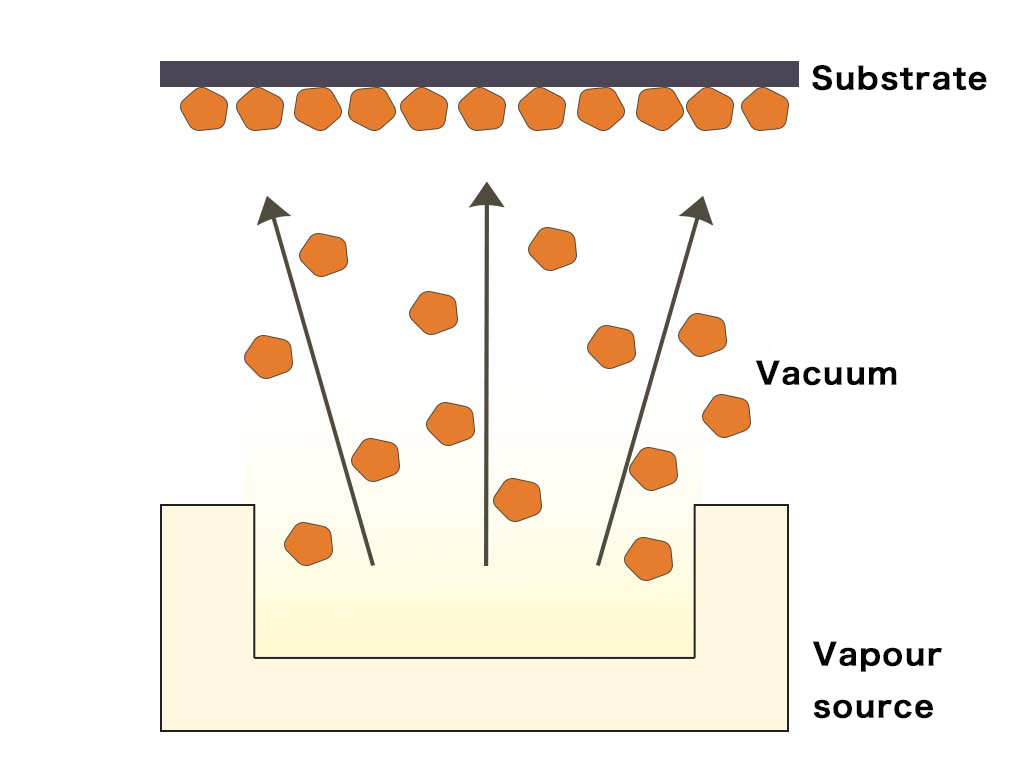
To understand the vacuum evaporation process, it is first necessary to understand the concept of ‘vapor’.
A familiar example of steam is water vapor.
This is a phenomenon in which a film of water adheres to the window glass when hot water is boiled in a closed room and the water evaporates, causing the glass to fog up.
The principle is applied to form thin films.
The key points of the evaporation method are the evaporation and vaporization sources.
In the vacuum evaporation method, the substance that forms the thin film as a vapor is called the evaporation source.
Actually, there are several types of heating methods for evaporation source, which can be divided into resistance heating deposition, electron beam deposition, hollow cathode deposition and high-frequency induction heating deposition.
Then, various deposition sources are used depending on the type of deposition material and application.
The material evaporated from the evaporation source reaches the substrate surface, where it condenses and solidifies to form a thin film.
Resistance Heating Deposition Source
A method that uses Joule heat to evaporate a substance to be made into a thin film.
This prevents diffusion from occurring on the substrate and allows the formation of dense thin films with excellent adhesion.
The problem is that it is difficult to control the film deposition rate.
Electron beam evaporation source
A technique whereby an accelerated electron beam is irradiated onto an evaporating material, which is then heated, vaporized and deposited on a substrate.
Since evaporation is performed by direct heating through irradiation of a high-energy electron beam to the evaporating material, metals and oxides with high melting points can be evaporated.
High-frequency induction heating evaporation source
A method of heating and evaporating material in a crucible by winding a high-frequency coil around an oxide crucible and using electromagnetic induction from high-frequency power applied to the coil.
As the crucible capacity can be increased, it is used in equipment for high-speed continuous deposition of metals such as aluminum.
Hollow cathode evaporation source
Source using hollow cathode discharge.
A large electric beam is extracted using a hollow (cavity) discharge, which can easily produce a large current, and is applied to thin film materials to form a film.
Advantages include low damage from plasma and heat to the substrate and suitability for low-temperature processing.
Used to deposit nitrogen films of titanium on electrical steel plates for TV displays, transformers and motors.
Summary
Various methods and equipment are used to form thin films, depending on the application and material.
In this article, one of the thin-film deposition methods, the vacuum evaporation method, was explained.