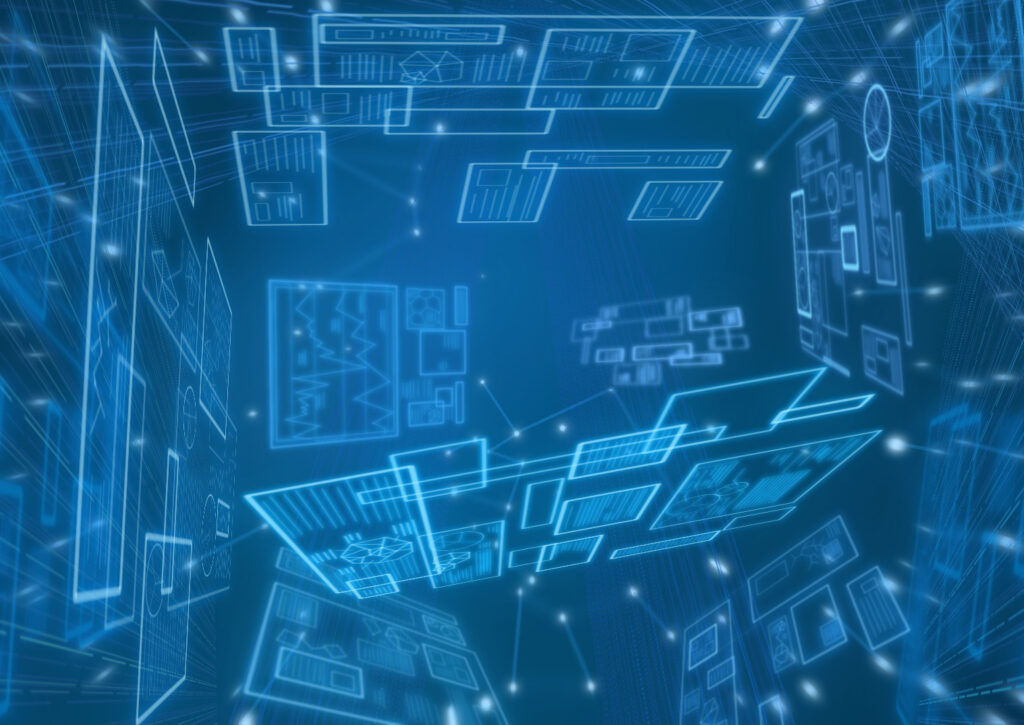
The SPS has various features such as short-time sintering, homogeneous sintering, microstructure control, and temperature gradient sintering, etc.
In this episode, we would like to introduce some specific applications of SPS sintering.
First, we will classify them as follows, including comparisons with conventional sintering methods, examples of microstructure control, and so on. Specific examples of each will be presented in the next episode.
(a)Comparison with and improvement of conventional sintering technology
Due to the effects of rapid temperature rise and ON/OFF pulse energization, SPS sintering provides sintered compacts with superior strength, hardness, etc. compared to conventional sintering technique
Sintering with SPS also makes it possible to produce sintered compacts with performance that could not be obtained with conventional sintering technique.
(b)Net-shape, near-net-shape sintering
The term “net shape” refers to the fact that after sintering, the product is finished without the need for processing. The term “near net shape” refers to a shape that is close to the finished product. Both of these methods reduce or completely eliminate post-processing after sintering, resulting in cost reduction, stable quality, and igh material yield, and are attracting attention as environmentally friendly production methods.
(c)Application for cutting/grinding tools
For cutting/grinding tools that use high-hardness materials such as diamond, deterioration of diamond due to high temperatures during sintering directly affects cutting/grinding performance. By taking advantage of the short-time sintering feature of SPS, hard materials such as diamond are densified without deteriorating, making it possible to manufacture tools with excellent cutting and grinding performance.
(d)Microstructure controlled sintering
In some functional materials such as dielectrics, grain size can play a significant role in the properties.
In the example of the dielectric properties of barium titanate, for which an appropriate grain size is required, neither too small nor too large to obtain the required properties, a grain size of 1-2 microns is optimal. By taking advantage of the short sintering time of SPS and optimization of heat-up rate and holding time, a sintered product with the required grain size and the required dielectric properties can be obtained.
(e) Examples of sintering functionally graded materials
The natural world is full of graded functional materials, such as bamboo, shells, and our skin. Japanese researchers have proposed the concept of Functionally Graded Materials (FGMs) as a new way to realize innovative properties and functions that cannot be achieved with conventional materials. Research and development is now being conducted with a focus on thermally stress-relaxed graded functional materials.
For example, there is a stainless steel and zirconia functionally graded material where one side is a stainless steel with the fine microstructure and properties of SUS340L, a metal, and the opposite side is a ceramic with the fine microstructure and properties of ZrO2.
(f)Simultaneous sintering of multiple pieces
This is one of the key technologies indispensable for achieving mass production and low cost.
There are multi-layer sintering in which multiple samples are sintered vertically in a sintering mold, multi-cavity sintering in which samples are arranged on a flat surface and composite multi-cavity sintering that combines these.
In all of these methods, homogenization of temperature and pressure is required in order to obtain a homogeneous sintered body.
Particularly, for temperature homogenization, multiple points of temperature measurement and diversification to the measured temperature control, etc. has been developed.
(g) Bonding and material synthesis other than sintering
There are examples of applications other than sintering using the SPS technology.
Typical example is bonding. There are variations in bonding methods such as solid/solid, solid/powder, solid/powder/solid, powder/powder, etc., and there are combinations of joining the same materials and different types of materials.
Unlike general welding and brazing, the entire surface is boded, and since no bonding materials like brazing is used, high heat resistance and high strength of the bonding surface can be obtained.
In some cases, the bonding strength exceeds the material strength.
Besides bonding, there are applications in material synthesis.
In addition to the synthesis of single crystal materials represented by the patent of Max Planck Institute in Germany, which succeeded in synthesizing single crystal materials, there are examples of application such as synthesis of eutectic and solidification molding of polyimide resin powder.
At the next episode, we would like to discuss specific examples of each of the applications.