放電プラズマ焼結装置(SPS)SPS(Spark Plasma Sintering) 焼結法またはPECS(Pulsed Electric Current Sintering) とも呼ばれる高エネルギー密度加工を応用した、高性能・高品質焼結を可能とする新世代の材料合成装置です。
SPS2000
経費を抑えて短時間で多様な実験をこなすことができる、大学や研究所でのR&Dに最適なエントリーモデルです。
POINT
- 省スペース(当社比1/2)
- 迅速な排気スピード
- オリジナルの多彩な機能搭載
本体寸法
W750mm×D1250mm×H1700mm
SPS温度 | 試料径 | DCパルス電源 | 1000 - 3000A |
---|---|---|---|
RT - 2500℃ | φ5 – 30mm | 1000 - 3000A | 30 – 70kN |
Smart SPS
SPS(放電プラズマ焼結)/ PECS(パルス電流焼結)は、省エネ/加工時間の短縮を可能とし、高品質の成果が得られることから長年注目されてきたユニークな材料合成技術(焼結/結合/表面処理、等)です。複合材料、先端金属材料、先端セラミック材料、磁性材料、FGM(傾斜機能材料)などの先端材料の研究開発はもちろんのこと、実際の製品の生産用にも用いられています。
この技術を使用すると、従来の焼結方法では焼結が難しい材料であっても、DCパルス電流を粉末/金型に直接通電することにより、高品質な(優れた特性や均一性を備えた)焼結成形体を得ることができるため、材料設計の柔軟性が向上します。このことから、SPS(PECS)は、機械部品や自動車・航空機用部品に使用される熱電・磁性・機能材料など、エネルギー・環境分野において飛躍的な進歩が期待されており、様々な分野で幅広く採用されています。
菅製作所は、SPSと当社独自の粉体表面処理システムのブランド製品を組み合わせたハイブリッド材料合成システムを「Smart SPSプロセス」として提供しています。
SAL1000(デスクトップ型ALD装置)
加工原理
SPS(Spark Plasma Sintering) 焼結法はPECS(Pulsed Electric Current Sintering) とも呼ばれる高エネルギー密度加工を応用した固体圧縮焼結法の一種です。粉体/ダイに直接DCパルス電流を通電することにより
効率的に必要な部分のみ加熱することで、ホットプレス法(HP)、熱間等方圧焼結法(HIP)、常圧焼結法(PLS)などの従来焼結法では焼結できない材料、あるいは高性能・高品質焼結を可能とする新世代の材料合成技術です。焼結・接合・合成・表面処理等の広範囲な材料合成加工法で室温から2000℃超の超高温領域での応用ができ、短時間加工・省エネルギー型加工を特徴としています。
粉末の材質、粒径、粒形などの特性、粉末表面の状態によっては
粒間で放電することもあり、放電部分がプラズマ状態になることから放電プラズマ焼結の名前が付い粒間で放電することもあり、放電部分がプラズマ状態になることから放電プラズマ焼結の名前が付いています。
放電の有無にかかわらず、高品質・高性能の材料の合成が可能であり、合成加工の応用範囲が広いこと、合成できる材料が幅広い分野であることから、たくさんの研究者・技術者が応用しており、まさに新世代の材料合成技術です。
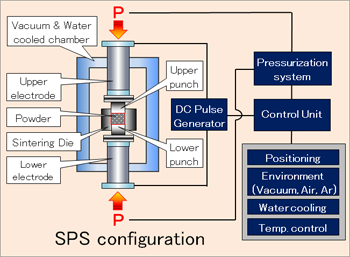
特徴
(1) 幅広い分野の新材料開発・生産への応用が可能です。高分子材料、金属、セラミックス、金属間化合物、複合材料系の材料合成(焼結・接合・合成・表面処理)に応用できます。
(2) 焼結技術の熟練・経験がなくとも材料の開発ができます。
焼結条件が広い範囲で選択可能であり、焼結条件を変更することで焼結体の性質・性能が変化します。条件を適切に設定することで、目的の性質・性能に近い材料を得ることが可能です。
(3) 難焼結材料に大きな威力を発揮します。強度の高い多孔質材料、活性の高いアルミニウム・チタンなどの金属、傾斜機能材料等の複合材料、焼結助剤なしの高温焼結材料等々従来焼結法ではできなかった材料合成が可能です。
(4) ON/OFFパルスDC電源を使用し、ON/OFFの条件を変えることで、粉体の微小領域の昇温・熱拡散による冷却の状態を変化させることができます。
前項で述べた広範囲の焼結条件との組み合わせにより、微細組織構造制御焼結を装置・SPSプロセスで行うことができます。
(5) 安全性が高く、操作性のよい設計としています。
短時間・大電流・高温の材料合成を安全に行えるように、各種インターロックを内蔵し、視認性・操作性の良いタッチパネルを採用することで、さらに安全に装置を制御・操作することができます。
(6) 耐久性が高く、堅牢な装置です。
長期間の連続使用に耐えるよう、高温装置の経験をベースにした構造・加工方法を採用しています。
(7) コンパクトな設計
限られたスペースで装置が使用でき、使いやすいコンパクトな装置となっています。
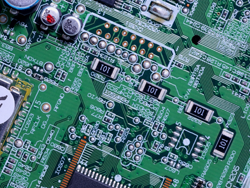
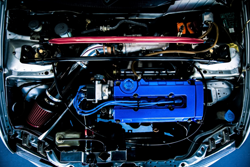
対象とする材料(例)
■金属系
Li, Be, Na, Mg, Al, Si, Ti, V, Cr, Mn, Fe, Co, Ni, Cu, Zn, Zr
Zr, Nb, Mo, Ru, Rh, Pd, Ag, Hf, Ta, W, Re, Ir, Pt, Au
■セラミックス系
酸化物:Al2O3,Mullite,ZrO2,MgO,SiO2,TiO2,HfO2,ZnO
炭化物:SiC,B4C,TaC,TiC,WC,ZrC,VC,HfC
窒化物:Si3N4,TaN,TiN,AlN,ZrN,VN
ホウ化物:TiB2,HfB2,LaB6,ZrB2,VB2
フッ化物:Lif,CaF2,MgF2
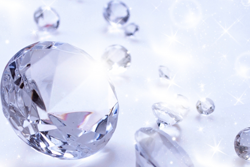
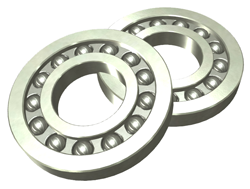
■複合材料系 傾斜機能材料(FGMs)
Si3N4+Ni,Al2O3+Ni,ZrO2+Ni,Al2O3+TiC,Al2O3+ZrO2
SUS+ZrO2,Al2O3+SUS,SiO2+SUS,Ti+SUS
SUS+WC/Co,BN+Fe,WC+Co+Fe,SUS/CU
■金属間化合物系
TiAl,MoSi2,Si3Zr5,NiAl,NbCo,Nb3Al,B6Si
Sm2Co17,NdFeB,FeAl
■ その他
有機系材料(ポリイミド他)、熱電材料、誘電体、光機能材料
実用化されたアプリケーション開発(例)
1. WC / Coダイヤモンド切断刃
2.伸線ダイス
3.金属結合ダイヤモンド研削工具
4. WC / Coダイヤモンドツール
5.セラミックノズル
6.非球面レンズガラス成形ダイ(バインダーレスWC)
7. Al-Si合金、自動車部品(ピストンヘッド)
8. Al-Si合金、アプライアンスコンポーネント(スクロール)
9. Ti-Al排気バルブ、自動車部品(金属間化合物)
10. ICリードフレームモールド(WC / Co、ハードメタル)
11.缶(乾電池)製造用の型抜き
12. WC / Coフィルムスリッター(ハードメタル)
13. EDM機械部品(WC / Co)の通電ブロック
14.ホモジナイザー(WC / Co、セラミック)
15.ブレーキディスク
16.半導体、ハードディスクなどのスパッタリングターゲット材
17. ZrO2セラミックスゲージブロック
18. Fe-Si合金コンポーネントロール(印刷用)
19.ベアリングメタル(SPS接合)
20.セラミックツール(複合材料)
21.プラスチック金型材料(固相拡散接合)
22.傾斜機能材料(WC / Co、ハードメタル)
23.透明セラミック
WC =炭化タングステン
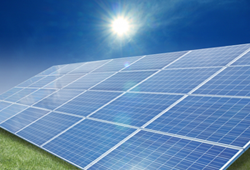
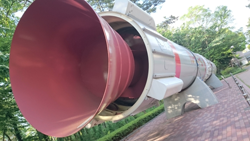
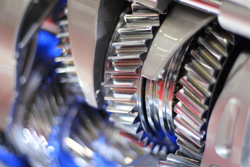
SPS2000仕様表
※大型試料の作成(大容量電源/加圧力)も可能です。別途お問い合わせください。
修理・改造
弊社装置に関わる保守サービスは、北海道の本社及び静岡県の拠点から技術者を派遣して対応致します。また、改造・保守に関わる事前お打合せについては北海道と関東地区に駐在している営業担当者にて対応致します。
装置の導入後も安心して装置をご使用頂けるよう体制を整えております。
装置の御納入後の定められた保証期間内は、弊社が定める一定の条件(天災や誤った使用方法に起因する故障)に含まれない初期不良等の不具合に対しては無償による修理対応を行います。 詳細はお問い合わせください。
サービスメニュー例
- ・装置の定期メンテナンス、不具合時のサービス対応
- ・装置の改造や機能追加、それらに伴うプログラムソフトの変更
- ・装置の移設、レイアウト変更
- ・オペレーショントレーニング(ユーザー様の運用担当者の交代時など)
- ・消耗品の購入