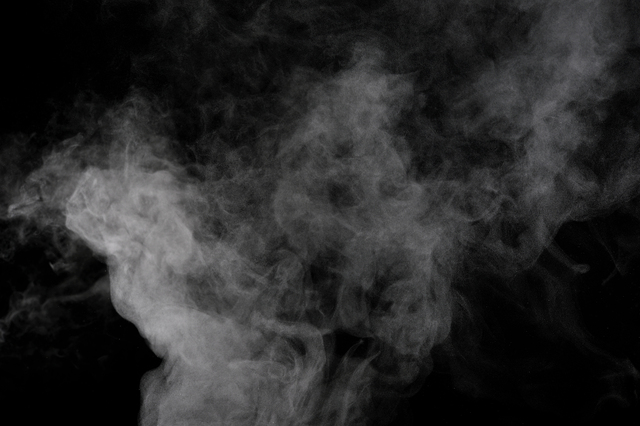
コーティング加工は製品の機能性を高めたり、機能を長く保持させたりする役割を持っています。製品の外側・内側には多くのコーティング技術が使われています。そのなかの代表例が「蒸着」です。
この記事では、スパッタ装置をはじめとする成膜装置を製作する菅製作所が、成膜の基本である「蒸着」の基本的な原理を解説するとともに、具体的な用途やスパッタ装置との違い、選び方のポイントなどを詳しく解説します。
目次
1.蒸着の基礎知識
①蒸着の原理と仕組み
「蒸着」とは簡単に言うと、ある物質を蒸発させて、その蒸気を別の物体の表面に当てて薄い膜を作る技術です。 このようにして作られた膜は、元の物体にはない性質を持たせることができます。
想像してみてください。お鍋に水を入れ、フタをして火にかけると、しばらくするとフタの内側に水滴がびっしり付きますよね。これは、水が熱せられて水蒸気になり、フタの冷たい面に触れて再び水に戻ったからです。
蒸着も同じような原理です。ただ、蒸発させるのは水ではなく、金属やガラスなどの様々な物質です。これらの物質を高温に加熱すると、気体になります。この気体を、例えばガラスやプラスチックなどの表面に当てると、冷えて固まり、薄い膜を作ります。この膜が、蒸着によって作られた膜なのです。
実際に蒸着は私たちの身の回りの製品にも使われている技術です。 例えば、メガネのレンズに施されている反射防止コーティングや、CDやDVDの記録面に光を反射させるためのアルミ膜などが、蒸着によって作られています。これらの膜は、非常に薄く、肉眼ではほとんど見えませんが、製品の性能を大きく左右する重要な役割を果たしています。
②蒸着で使用する代表的な材料
蒸着で使用する材料は、その用途や求められる特性によって多岐にわたります。代表的な材料を以下にまとめます。
金属 | アルミニウム銅チタン銀金 |
---|---|
セラミック | 酸化アルミニウム:二酸化ケイ素酸化マグネシウム |
有機物 | ポリマー蛍光色素有機薄膜トランジスター(OFT) |
半導体 | シリコンガリウムインジウムカドミウムセレン |
③蒸着の種類
蒸着には「物理蒸着」と「化学蒸着」の2種類があります。
③-①物理蒸着(PVD)
物理的反応を利用して対象物に皮膜を形成する工法になります。一般的に「真空蒸着」「スパッタリング」「イオンプレーティング」に分類されています。
真空蒸着 | 真空状態の装置の中で金属を熱して蒸発させ、その蒸気を対象物の表面に当てて薄い膜を形成する技術です。まるで、お鍋の水が沸騰してフタの内側に水滴がつくように、金属を蒸発させて対象物に付着させるイメージです。 |
---|---|
スパッタリング | 真空状態の装置の中で、金属に高エネルギーの粒子を衝突させて、その金属の微粒子を対象物の表面に付着させ、薄い膜を作る技術です。石を砂場に投げつけたときに飛び散った砂が、対象に付着するイメージです。 |
イオンプレーティング | 真空蒸着と似ていますが、より強力で密着性の高い膜を形成できる点が大きな特徴です。真空蒸着では、単に金属を蒸発させて対象物に付着させますが、イオンプレーティングでは、蒸発した金属の粒子にプラスの電荷を与え、対象物にマイナスの電荷を与えることで、まるで磁石が鉄を引きつけるように、金属の粒子が対象物に強く引きつけられます。 |
菅製作所では、ご要望に応じてスパッタリング装置をカスタマイズすることが可能です。ご予算・ご要望・用途をお伝えいただければ、最善のご提案ができますので、お気軽にご相談ください。(実績についてはこちら)
③-②化学蒸着(CVD)
化学蒸着とは、気体状の物質を反応させて、その反応生成物を対象物の表面に付着させることで薄膜を形成する技術です。化学蒸着は、半導体製造のほか、太陽電池、ディスプレイ、光学素子など、様々な分野で利用されています。
④蒸着で使う主な装置
特徴 | 原理 | 用途 | |
真空蒸着装置 | シンプル、低コスト、様々な材料に対応 | 加熱による蒸発 | 光学薄膜、装飾膜など |
スパッタリング装置 | 密着性が高い、均一な膜 | アルゴンイオンによるスパッタリング | 半導体製造、ハードディスクなど |
MBE装置 | 高品質な結晶膜、原子レベルの制御 | 分子線のエピタキシャル成長 | 半導体デバイス |
アーク蒸着装置 | 高融点材料に対応、高速度成膜 | アーク放電によるプラズマ生成 | 耐熱コーティング、装飾膜など |
2.蒸着の用途例
蒸着は、その高い汎用性から、私たちの身の回りの様々な製品に利用されています。
①電子機器
- ディスプレイ:スマートフォン、タブレット、テレビなどのディスプレイには、高精細で鮮やかな画像を実現するために、蒸着技術が用いられています。特に、有機ELディスプレイでは、発光層の形成に蒸着が不可欠です。
- タッチパネル:スマートフォンやタブレットのタッチパネルには、導電性の高い金属膜を蒸着することで、タッチ操作を実現しています。
- 半導体:集積回路の製造プロセスにおいて、絶縁膜や導体膜の形成に蒸着が使われています。
②光学製品
- 眼鏡レンズ:レンズの表面に反射防止膜や防汚膜を蒸着することで、視界をクリアにし、レンズの寿命を延ばしています。
- カメラレンズ:レンズの表面に多層膜コーティングを施すことで、光の反射を抑え、高画質を実現しています。
- 望遠鏡:望遠鏡の鏡面には、高反射率の金属膜を蒸着することで、集光効率を高めています。
③その他
- 装飾品:ジュエリーや時計の文字盤など、装飾品に光沢や色を出すために蒸着が利用されています。
- 自動車:自動車のパネルやヘッドライトには、耐傷性や耐久性を高めるための蒸着が行われています。
- 食品包装:食品の鮮度を保つために、包装材にバリア性を高める蒸着が施されています。
3.蒸着が使われているコーティング例
蒸着技術は、その高い汎用性から、様々な種類のコーティングに用いられています。以下に、代表的なコーティングの種類と、それぞれの特長について詳しく解説します。
①撥水・防汚コート
フッ素化合物などの低表面エネルギー物質を薄くコーティングすることで、水や油などの液体が表面に広がらず、玉状になって転がり落ちるようにします。
【特徴】
- 高い撥水性・防汚性: 水や油汚れが付きにくく、簡単に落とせるため、清掃の手間を軽減できます。
- 滑り性向上: 表面の摩擦抵抗を低減し、滑らかな手触りを実現します。
- 耐久性向上: 表面を保護し、摩耗や傷から守ります。
- 用途: スマートフォンの画面、自動車のボディ、建物の外壁など、様々な製品に利用されています。
組み合わせ: ARコートやミラーコートとの組み合わせにより、撥水性だけでなく、反射防止や高い光沢といった機能も同時に実現できます。
②増反射コート(ミラーコート)
多層膜を蒸着することで、光の波を干渉させ、特定の波長の光を強く反射させます。
【特徴】
- 高い反射率: 鏡のような高い反射率を実現できます。
- 装飾効果: 製品に深みのある光沢を与え、高級感を演出できます。
- 用途: 鏡、装飾品、光学機器など、高い反射率が求められる製品に利用されています。
③金属コート
金属材料を蒸着することで、基材の表面に金属膜を形成します。
【特徴】
- 高い導電性・熱伝導性: 電子部品や熱交換器などに利用できます。
- 装飾効果: 金属特有の光沢や色合いにより、製品の外観を向上させます。
- 耐摩耗性・耐熱性: 工具や金型など、過酷な環境で使用される製品の耐久性を向上させます。
- 用途: 電子部品、装飾品、工具、金型など、幅広い分野で利用されています。
④ARコート(反射防止コート)
多層膜を蒸着することで、光の波を干渉させ、反射光を打ち消し合うようにします。
【特徴】
- 高い透過率: 光の反射を低減することで、透過率を高め、視認性を向上させます。
- 映り込み防止: 表面の映り込みを抑制し、クリアな視界を実現します。
- 表面保護: 表面を保護し、傷や汚れから守ります。
- 用途: 眼鏡レンズ、カメラレンズ、ディスプレイなど、光の透過率が重要な製品に利用されています。
4.蒸着とスパッタの違い
「蒸着とスパッタの違いはなんだろう?」は、成膜について考えるうえでよくぶつかる疑問です。この記事では、あえて独立したトピックとして取り上げ、あらためて両者の違いや選び方のポイントについて説明します。
①仕組みの違い
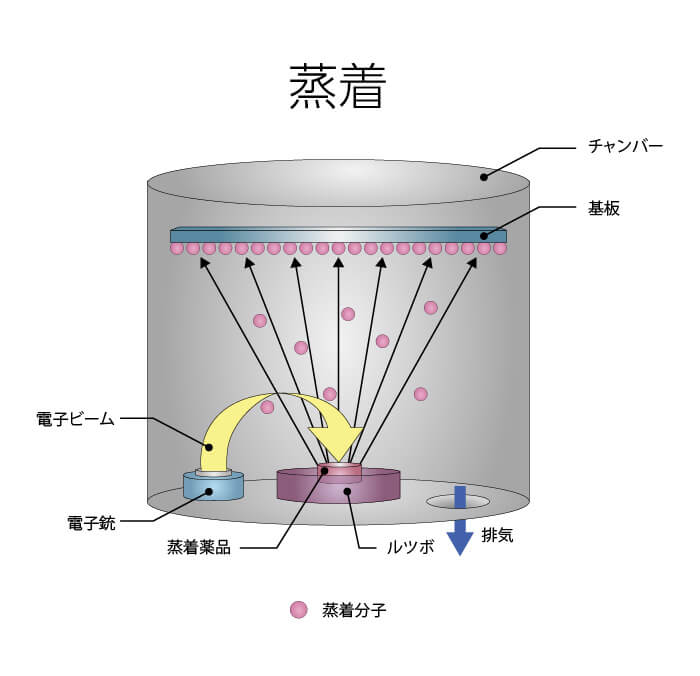
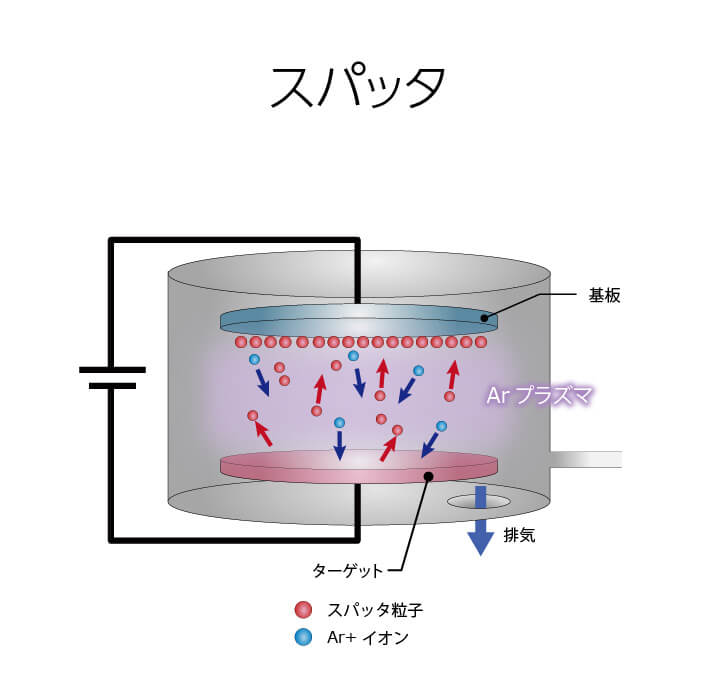
②蒸着とスパッタのメリットと注意点の比較
蒸着のメリット・注意点
【蒸着のメリット】
- 高速度成膜: スパッタリングに比べて、数倍の速さで薄膜を形成することができます。そのため、生産性の向上が期待できます。
- 装置の簡素化と低コスト: 装置の構造が比較的シンプルであるため、導入コストを抑えることができます。
- 膜厚の精密制御: 蒸着速度を調整することで、製品に合わせて膜厚を精密に制御できます。
- 高純度膜の形成: 高真空環境下で蒸着を行うため、高純度の薄膜を形成できます。
低温プロセス: 常温またはそれに近い温度で加工できるため、熱に弱い基材にも対応可能です。
【蒸着の注意点】
- 組成変化: 一部の材料では、蒸発過程で組成が変化し、膜の特性が元の材料と異なる場合があります。
- 付着力の弱さ: 粒子のエネルギーが小さいため、基板への付着力が比較的弱く、耐久性が低い場合があります。
- 大面積への対応の難しさ: 一般的に、大面積の基板への均一な成膜は困難です。ただし、装置の改良やプロセス条件の最適化により、大面積への対応も可能です。
- 高融点材料への対応の難しさ: 抵抗加熱式蒸着では、高融点の材料を蒸発させることが困難です。電子ビーム蒸着など、より高エネルギーな加熱源が必要となります。
スパッタのメリット・デメリット
【スパッタリングのメリット】
- 高い付着力: 粒子が大きなエネルギーを持って基板に衝突するため、基板との密着性が非常に高く、耐久性のある膜を形成できます。
- 組成の再現性: 合金や化合物などの複雑な組成の材料でも、ターゲットの組成をほぼそのまま膜に転写することができます。
- 高融点材料への対応: 高融点の材料もスパッタリングによって薄膜化できるため、幅広い材料に対応可能です。
- 膜厚の精密制御: スパッタリング時間を調整することで、ナノメートル単位での膜厚制御が可能です。
- 大面積への均一成膜: 大面積の基板にも均一な膜を形成することができ、生産性に優れています。
【スパッタリングの注意点】
- 基板形状の影響: 基板表面の凹凸や粗さによって、膜の厚みや組成が均一にならず、膜質が劣化する場合があります。
- 低速成膜: 蒸着に比べて成膜速度が遅いため、生産性が低い場合があります。
- プラズマダメージ: プラズマによるダメージで、基板や膜が損傷する場合があります。特に、有機材料や半導体など、プラズマに弱い材料には注意が必要です。
- 高コスト: スパッタリング装置は高価であり、真空チャンバーの維持管理にも費用がかかります。また、スパッタリングガスやターゲット材料の費用も考慮する必要があります。
- 材料の制限: 一部の材料は、スパッタリングに適さない場合があります。例えば、有機材料はプラズマによって分解される可能性があります。
③蒸着とスパッタを選ぶ際のポイント
以上みたように、蒸着とスパッタは、どちらも薄膜形成に用いられる重要な技術ですが、それぞれの特性が異なるため、用途や目的に合わせて適切な方法を選択することが重要です。
以下に選択のポイントをいくつか整理しました。ぜひ参考にしてください。
膜の特性
密着性 | 高い密着性が要求される場合はスパッタが適している。 |
---|---|
組成 | 合金や化合物を均一に再現したい場合はスパッタが適している。 |
膜厚 | 精密な膜厚制御が必要な場合は、どちらの方法でも可能。 |
基板の形状
平面 | 両方とも対応可能。 |
---|---|
凹凸 | 蒸着は凹凸のある基板には不向きな場合がある。 |
材料
高融点材料 | スパッタの方が適している。 |
---|---|
有機材料 | 蒸着の方が適している場合がある。 |
生産性
高速成膜 | 蒸着が適している。 |
---|---|
大面積 | スパッタが適している。 |
コスト
装置コスト | 相対的に蒸着の方が低コスト。 |
---|---|
ランニングコスト | 同上。 |
5.菅製作所のスパッタ装置はご要望に合わせてカスタマイズできます
菅製作所はお客様の細かいニーズにお応えするべく、綿密なヒアリングと研究理解を徹底し、用途に合わせてカスタマイズしたスパッタ装置を提案しています。
- 設置スペースが限られている
- 用途が限定的
- 費用をかけず自分たちでメンテナンスがしたい
- 学生でも使える使いやすさがほしい
- 現場の細かい状況・事情を汲み取ってカスタマイズしてほしい
このようなご要望をお持ちの方は、ぜひ一度、お気軽にご相談ください。
まとめ
この記事では、蒸着の原理や仕組み、種類、用途を詳しく解説しました。蒸着は、私たちの身の回りの様々な製品に利用されており、その高い汎用性から、今後もますます重要な技術となるでしょう。
特に、スパッタリングとの比較では、それぞれのメリット・デメリットを明確にし、具体的な用途や選択のポイントを解説しました。
蒸着は、真空蒸着やスパッタリングなど、様々な方法がありますが、菅製作所では、お客様のご要望に合わせてカスタマイズ可能なスパッタリング装置を提供しています。
成膜に関するお悩みやご質問がございましたら、お気軽にご相談ください。
【参考】