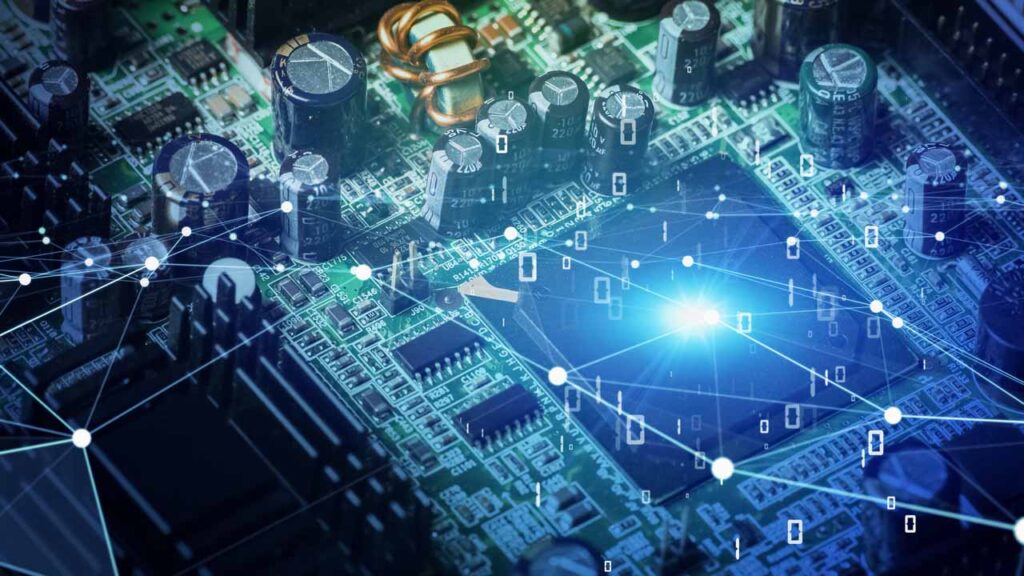
現代のハイテク製品に不可欠な「薄膜」を生み出すスパッタ成膜技術。その名は知っていても、具体的な仕組みや種類、そして導入時のポイントまで深く理解している方は少ないかもしれません。本記事では、スパッタリングの基礎の基礎から、そのメリット・デメリット、多岐にわたる成膜材料、そしてプロセスにおける課題と解決策、さらには最適な装置選びの秘訣まで、徹底的に解説します。
スパッタ成膜の導入や品質向上でお悩みの企業様へ。本記事で得られる知識が、貴社の技術革新の一助となれば幸いです。ご不明な点や具体的なご相談は、ぜひお気軽にお問い合わせください。
▶お問い合わせはこちら
目次
スパッタ成膜(スパッタリング)とは何か?
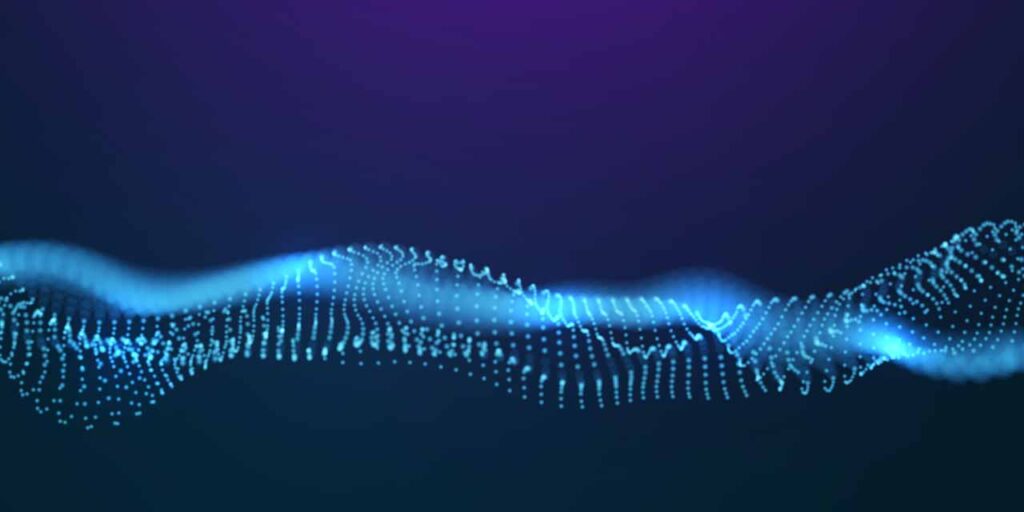
スパッタリング成膜の定義
スパッタリング成膜とは、真空中でターゲット材料にアルゴンイオンなどの粒子を高速で衝突させ、弾き飛ばされたターゲット材料を基板上に堆積させて薄膜を形成する技術です。この現象自体は1850年代に観察され、1960年代には量産・工業製品にも用いられるようになりました。
スパッタリング成膜の代表的な材料
スパッタリングは、高融点金属や合金、化合物など、幅広い種類の材料で成膜が可能であり、真空蒸着法では成膜が困難な材料にも対応できます。
スパッタリングの成膜材料の代表例としては、以下のものが挙げられます。
金属 | Cr(クロム)、Cu(銅)、Ti(チタン)、Ag(銀)、Pt(プラチナ)、Au(金)など。 |
合金 | Ni-Cr(ニッケル-クロム)、SUS(ステンレス)、Cu-Zn(銅-亜鉛)など。 |
酸化物 | ITO(酸化インジウムスズ)、SiO2(二酸化ケイ素)、TiO2(二酸化チタン)、Nb2O5(五酸化ニオブ)、ZnO(酸化亜鉛)など。 |
これらの材料は、ターゲットと呼ばれるプレート状の成膜材料として使用されます。
条件変更が成膜結果に与える影響
スパッタリングのメカニズムが理解できると、スパッタリングのパラメーターを変えた時の変化を定性的に予測できるようになります。
例えば、ターゲット材料を非磁性材料から鉄やニッケルなどの磁性材料に変えた場合、通常ターゲットの外に出てほしい磁力線がターゲットの中を通ってS極に入ってしまい、磁力線が外に出てこない現象が発生することがあります。
これに対応するためには、ターゲット材料を薄くしたり、フェライト磁石ではなくより強いサマリウムコバルト磁石やネオジム磁石などの磁石に取り替えて磁力線を強化し、外に磁力線を出す方法が取られます。
スパッタリングターゲットとは
スパッタリングターゲットとは、スパッタリングによって薄膜形成を行うための材料のことです。
ターゲットには、以下のような条件が求められます。
- 不純物が少ない材料であること
- 高密度で内部に気泡を含まないこと
- 膜厚の均一性、膜質の均質性が保てる素材であること
- 生産する際に価格が予算内であること
これらの条件を満たした上で、用途別にターゲットが変更されます。ターゲットの種類によって向き・不向きがあり、付与できる特性や強度などに応じて選定する必要があります。
選定ポイントとしては、反りが小さいものを選ぶこと、そして強度が高いものを選ぶことが挙げられます。
例えば、金属系の粘性がある材料は反りに強いですが、シリコンやセラミックスのような固くて割れやすいものは反りに弱い傾向があります。冷却方式で「直接冷却」を使用する場合は、水圧がかかり続けるため、強度が弱いターゲットは変形や剥がれが起こる可能性があるため、強度が重要になります。
スパッタと蒸着の違い
蒸着成膜は蒸着材料を加熱し、気化させることで離れた位置に置かれた対象物に 蒸着材料を付着させ薄膜を形成します。
一方スパッタリング成膜とはターゲット材料にプラズマ化したアルゴンイオンを高エネルギーで衝突させ、結果、弾き飛ばされたターゲット材料の微粒子が離れた位置に置かれた対象物に付着し薄膜を形成します。
蒸着に比べ膜厚を緻密に制御できること、膜の密着力が強い利点があります。また融点が高く気化させにくい金属やそれぞれの金属の融点が異なる合金の成膜も組成率を変えることなく可能になります。
スパッタ成膜のメリットとデメリット
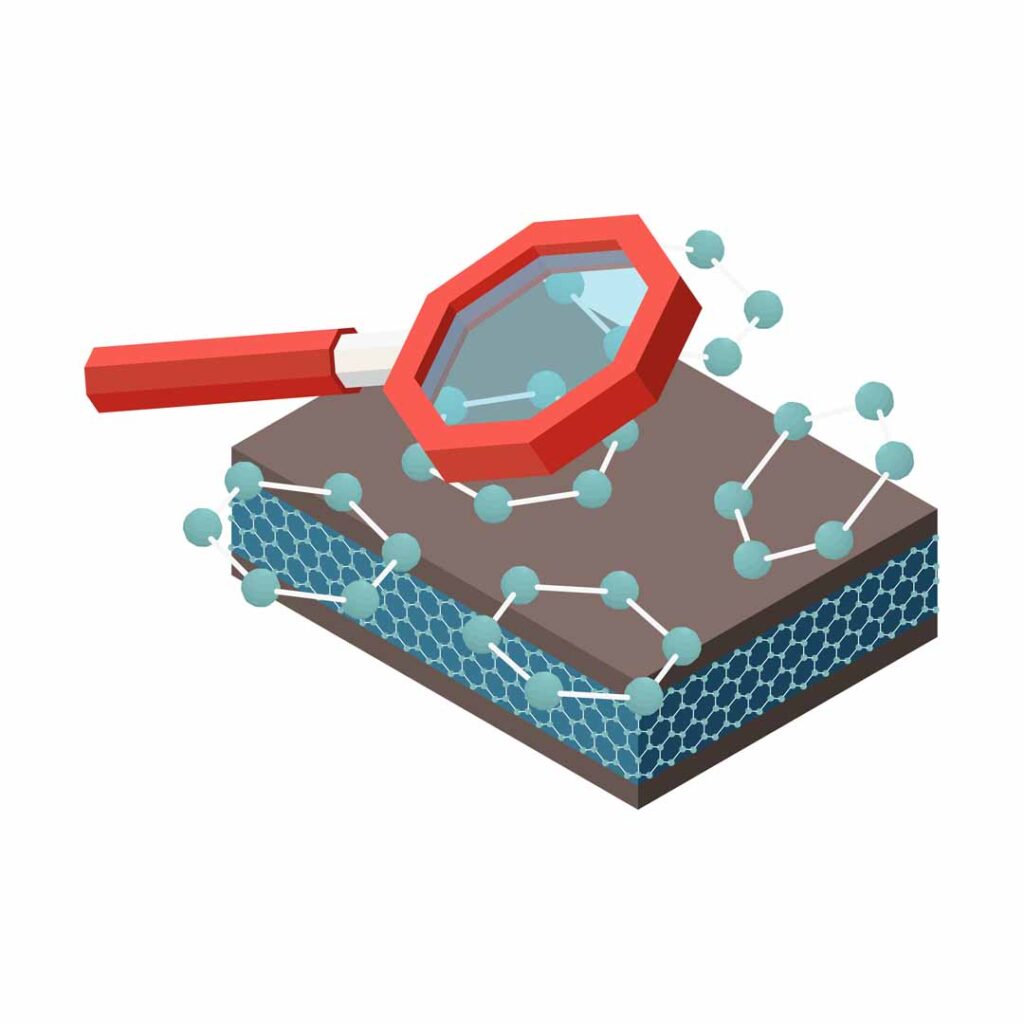
ここでは、スパッタ成膜のメリットとデメリットを解説します。
スパッタ成膜のメリット
- 付着力が強い
- 原料の組成比が変化しない
- 高融点の原料でもコーティングできる
- 平面であれば大きな面積でも均一に膜が作成できる
- 時間により膜厚のコントロールができる
スパッタ成膜はなんと言ってもやはり均一な膜が形成できることと、高い密着性により安定した製品製造ができる点が魅力です。
スパッタ成膜のデメリット
- 凹凸のある対象物には向かない
- 成膜に時間が必要
- プラズマによる製品の影響が起こる場合がある
- 電源が高価かつメンテナンスが必要
- 材料によってはコーティングできない
スパッタ成膜は立体物へのコーティングには向きません。また、スパッタ装置は精密機械であるためメンテナンスが必須で、費用も高額になりやすい点がネックです。
スパッタリングの種類
スパッタリングは様々な種類があり、それぞれ異なる特徴と弱点を持っています。ここでは主要なスパッタリング法について解説します。
①2極スパッタリング法
もっとも基本的なスパッタリング方式です。
▶特徴
- 構造のシンプルさ
装置構造が比較的シンプルで、導入しやすい。
- 基本的な成膜
基板を陽極、成膜材料(ターゲット)を陰極として薄膜を形成します。
▶弱点
- 成膜速度が遅い
プラズマを安定的に発生させるために多くのガス導入が必要となり、成膜速度が比較的遅いです。
- 基板の温度上昇
スパッタリング時に発生する二次電子が基板に衝突し、基板が高温になりやすいです。これにより、熱に弱い基板へのダメージや、膜質の変化が起こる可能性があります。
- 不純物混入のリスク
比較的低い真空度で動作するため、残留ガスが薄膜に混入しやすい傾向があります。
②マグネトロンスパッタリング法
2極スパッタリング法の課題を改善するために開発された方式です。
▶特徴
- 高速成膜
ターゲットの近くに磁石を配置し、磁場によって電子を閉じ込めることでプラズマ密度を高めます。これにより、ターゲットへのイオン衝突効率が向上し、成膜速度が大幅に向上します。
- 基板への熱ダメージ軽減
電子をターゲット近傍に閉じ込めるため、基板への二次電子の衝突が減り、基板の温度上昇が抑えられます。
- 高効率
少ないガス量で高密度プラズマを生成できるため、ターゲット利用効率も向上します。
▶弱点
- ターゲット利用効率の偏り
磁場によって電子が閉じ込められる領域(レーストラック)にプラズマが集中するため、ターゲットの特定の領域だけが消費されやすく、ターゲット全体の利用効率が悪くなることがあります。
- 装置構造の複雑化
磁石や磁場制御機構が必要となるため、2極スパッタリング法よりも装置構造が複雑になります。
③DCスパッタリング
直流電源を用いるスパッタリング法です。
▶特徴
- 導電性材料への適用
主に金属などの導電性ターゲット材料の成膜に適しています。
- 高速成膜
一般的にRFスパッタリングよりも成膜速度が速いです。
- コスト効率
装置コストやランニングコストがRFスパッタリングに比べて比較的低いです。
- 合金や化合物の組成維持
ターゲットの組成比をほぼそのまま薄膜に転写できるため、合金や化合物の成膜に適しています。
▶弱点
- 絶縁性材料への不適用
ターゲットが絶縁体の場合、プラス電荷(イオン)がターゲット表面に蓄積し、「チャージアップ」現象を起こして放電が停止してしまいます。そのため、絶縁性材料の成膜には適していません。
- 基板加熱
高エネルギーのイオンが基板に入射するため、基板の温度上昇が起こりやすい場合があります。
- 膜質の最適化
複雑な膜特性を得るためには、電力、圧力、ガス組成など多くのパラメータの最適化が必要で、時間と専門知識を要します。
④RFスパッタリング
高周波(Radio Frequency)交流電源を用いるスパッタリング法です。
▶特徴
- 絶縁性材料への適用
ターゲットに交流電圧を印加することで、チャージアップを防ぎ、SiO2やAl2O3などの絶縁性ターゲット材料の成膜が可能です。これがDCスパッタリングとの最大の差別化点です。
- イオンアシスト効果
基板には常にイオンが入射するため、イオンアシスト効果により緻密で高品質な薄膜が得られやすいです。
- 半導体産業での重要性
絶縁膜の成膜が可能なため、半導体デバイス製造において非常に重要な役割を担っています。
▶弱点
- 成膜速度が遅
一般的にDCスパッタリングと比較して成膜速度が遅い傾向にあります。
- 装置コストが高い
RF電源に加え、インピーダンスマッチングユニットが必要となるため、DCスパッタ装置に比べて高価になりやすいです。
- 複雑な調整
マッチングユニットの調整が必要となるなど、装置の操作がDCスパッタリングよりも複雑になることがあります。
- 基板へのダメージの可能性
T/S間(ターゲット-基板間距離)が短いと、プラズマによる基板へのダメージが発生する可能性もあります。
⑤反応性スパッタリング
スパッタリングガスに反応性ガスを混合して成膜を行う方法です。
▶特徴
- 化合物膜の形成
ターゲット材料と導入した反応性ガスが反応することで、酸化物、窒化物、炭化物などの様々な化合物薄膜を形成できます。例えば、金属ターゲットと窒素ガスで窒化膜、酸素ガスで酸化膜を作製できます。
- 膜組成の調整
反応性ガスの流量や分圧を調整することで、膜の組成や特性(硬度、光学特性、電気特性など)を細かく制御できます。
- 比較的低温成膜
高融点の化合物も比較的低い温度で成膜できるため、基板材料の制約が少ないです。
- 大面積・均一成膜
工業生産にも向いており、大面積でも均一に成膜が可能です。
▶弱点
- プロセス制御の複雑さ(ヒステリシス)
反応性ガスの導入により、ターゲット表面に化合物が形成され、スパッタリングレートが急激に変化する「ヒステリシス現象」が起こることがあります。これを避けるためには、ガス流量や分圧の精密な管理が必要です。
- 成膜速度の低下
ターゲット表面の化合物層の形成により、純粋なスパッタリングと比較して成膜速度が低下することがあります。
- ターゲットの「被毒」
ターゲット表面が反応性ガスによって完全に化合物化されると、スパッタリング効率が著しく低下し、プロセスが不安定になる「ターゲット被毒」が発生することがあります。
⑥ECRスパッタ (ECRプラズマスパッタ)
電子サイクロトロン共鳴(ECR)を利用して高密度プラズマを生成するスパッタリング法です。
▶特徴
- 高真空成膜
通常のスパッタ法よりも高い真空度で成膜できるため、薄膜への不純物混入が極めて少ないです。
- 低プラズマダメージ
基板が直接プラズマに曝されにくい「リモートプラズマ」方式であるため、基板へのダメージが非常に小さいです。熱に弱い基板や、ダメージを嫌う精密なデバイスの成膜に適しています。
- 緻密で均一な膜質
高密度プラズマと低ダメージ成膜により、非常に緻密で均一な薄膜が得られます。
- ターゲットの導電性不問
マイクロ波によりプラズマを生成するため、ターゲットの導電性を問わずスパッタが可能です。
- 優れた膜特性制御
ECRプラズマの高いイオン化効率により、低ガス流量でも高酸化度の薄膜が得られるなど、膜特性の制御範囲が広いです。
▶弱点
- 装置構造が複雑で高価
マイクロ波源や磁場印加機構が必要となるため、他のスパッタ装置に比べて構造が複雑で、導入コストが高価になります。
- ターゲットの状態管理
ターゲットの状態(特に酸化状態など)をモニターし、安定したプロセスを維持するためのノウハウが必要です。
- マイクロ波導入窓の汚染
金属や強還元性材料を成膜する際、マイクロ波導入窓にこれらの材料が付着すると、マイクロ波の透過が妨げられる問題が発生することがあります。
スパッタリングの成膜プロセス
STEP1:真空引きとアルゴンガス導入
まず、基板をセッティングした後、チャンバーのハッチを閉めて真空引きを行います。大気圧(10の+5乗パスカル台)から、スパッタリングに必要な10の-3乗から10の-4乗パスカル台まで真空度を高めます。
その後、スパッタリングに一般的に用いられるアルゴンガスをチャンバー内に導入します。アルゴン(原子番号18番)は、K殻に2個、L殻に8個、M殻に8個の合計18個の電子を持ち、最外殻に8個の電子があるため化学的に非常に安定している貴ガスです。他の物質と反応しづらく、大気中にも微量に含まれており収集が容易なため広く用いられます。
STEP2:RF電源の印加とプラズマ生成
アルゴンガスを流し始める前に、RF電源(高周波電源)を低めの電力(約30Wなど)でオンにします。これにより、ターゲット表面に13.56MHzの高周波電圧が印加されます。
このRF電圧はアルゴン原子の電子と陽子をバラバラにさせようとする力を加えますが、これだけではプラズマ状態にするのは困難です。
ここで、カソード内部に組み込まれている磁石が重要な役割を果たします。磁石はターゲット表面に磁力線を発生させるように設計されており、RF電圧で加速された電子がフレミングの左手の法則によって磁力線の周りを回転運動します。
この回転運動によって電子の移動距離が増加し、他のアルゴン原子に衝突しやすくなります。この衝突により電離と呼ばれる現象が発生します。電離では、アルゴン原子に電子が衝突することで、元の電子に加え、原子からさらに1個の電子が飛び出し、電子1個分の電荷がプラスになったアルゴンの陽イオン(アルゴンプラス)が誕生します。
飛び出した電子が再び磁力線の周りを回転し、別のアルゴン原子に衝突・電離を繰り返すことで、陽イオンと電子が束縛されずに飛び回る状態が維持されます。このような状態を、固体・液体・気体に続く「第4の状態」であるプラズマ状態と呼びます。マグネトロンスパッタ装置では、ターゲット表面にプラズマの光がドーナツ状に確認でき、これは磁場が水平になっている部分に衝突電離するアルゴン原子が集中するためです。
STEP3:Vdc電圧の発生とアルゴン陽イオンの加速
プラズマによって比較的自由に飛び回れるようになった電子がカソード(ターゲットが乗っている電極)に流入すると、カソードの直流的な電位がマイナスに大きく下がります。この時のカソードの電圧をVdcと呼びます。
このマイナスに下がったVdc電圧に引きつけられて、プラズマ中で生成された重いアルゴン陽イオン(アルゴンプラス)がターゲットに向けて加速されます。電子は軽く、陽子(イオン)は重いため、この重いアルゴン陽イオンが高速でターゲットに打ち付けられることになります。
STEP4:ターゲットのスパッタと成膜
加速されたアルゴン陽イオンがターゲット材料に衝突すると、ターゲット材料が粉々に飛び散ります。
飛び散ったターゲット材料が基板に到達し、付着・堆積することで、ターゲット材料の膜が基板上に形成されていきます。
▼動画で解説「スパッタリング成膜のメカニズム」
スパッタリングによる膜形成のプロセスを、動画で視覚的にイメージできます。ぜひ参考にしてください。
ガスの種類と圧力の役割
主に使用されるガスは、不活性ガスと呼ばれるものです。不活性ガスは反応性が低く、他の物質と化学的な反応を起こしにくいことから酸化を防ぐ・真空状態を維持するなどの目的で使用されます。
代表的な不活性ガスは「アルゴン」や「キセノン」が用いられることが多いです。アルゴンについては以下の記事で詳しく解説しています。
基板の材質と表面処理の重要性
基板の材質と表面処理も重要になります。
材質は基板の物理的な強度、硬さ、伝導性などに影響を与えるため、適切な基板を選ばなければ不安定な処理や故障の原因になります。一般的にはシリコン基板が用いられることが多いです。
表面処理については、薄膜の密着性や均一性を保つため重要な処理になります。特に半導体分野では繊細な制御が求められるため、表面処理とスパッタ成膜の組み合わせて薄膜を作る必要があります。
成膜の品質とコントロール
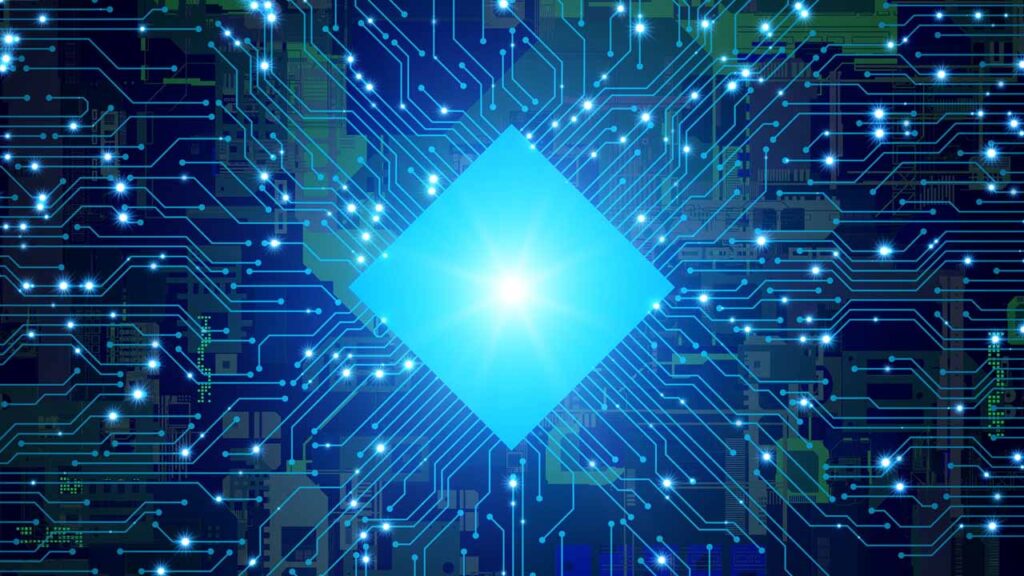
成膜の品質は、回路の動作に直結します。
薄膜を作成することで、電流をコントロールできるようになりますが、これには薄膜の厚さと均一性が重要になります。
電気を通すように薄膜を作成した場合、膜が厚過ぎれば電気が通りにくく、膜が薄過ぎれば電気が通り過ぎてしまいます。
膜が不均一に張られていると、一部は電気を通すけれど所々電気が通らない部分があるなど、思うように製品が動作しません。
成膜を均一にしながら厚さを適切にしなければ、狙った効果が得られないということです。
そのため、品質を向上させるためには、スパッタ装置の出力パワーや処理時間が重要となり、ナノスケールの薄膜に影響する技術であるため高価になりやすい特徴があります。
スパッタ成膜の課題と対策
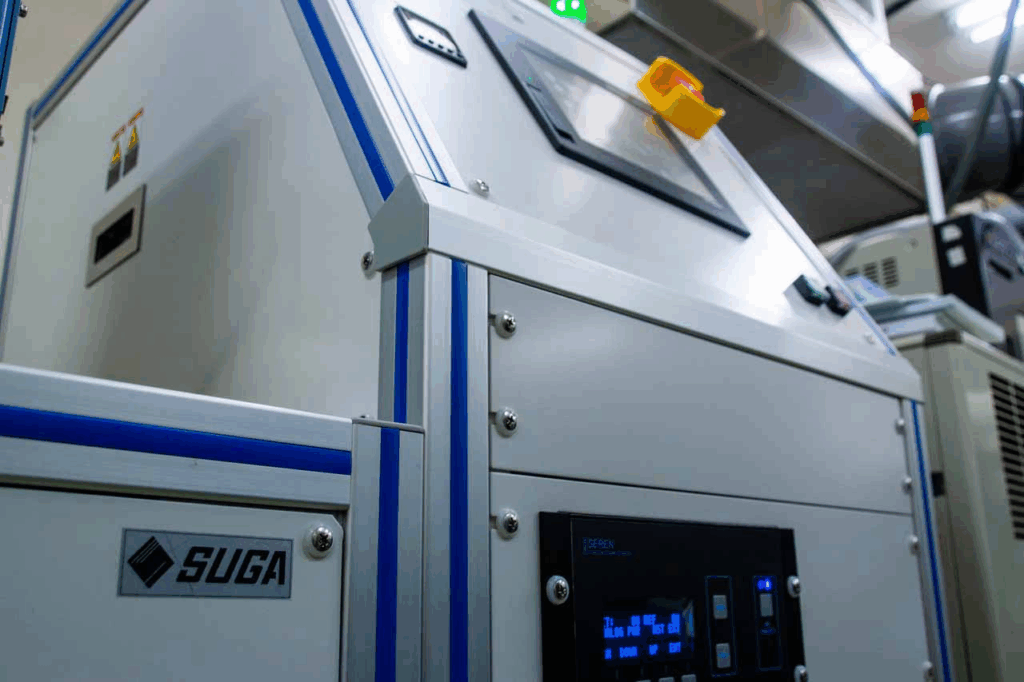
スパッタ成膜には、成膜中に発生する問題などに課題があります。
成膜中に発生する問題への対処法
スパッタ成膜では、成膜中に特定の問題が起こり得ます。例えば、基盤の温度が上昇することで制御が難しくなること、ターゲットの劣化により膜の成分や品質に影響が出るなど。
こういった問題へ対処するためには大きく二つの視点が必要です。一つは、そもそもスパッタ装置のスペックが足りているか、もう一つは保守管理を行なっているかです。
菅製作所ではスパッタ装置に複数のモデルを用意しており、800℃まで基盤が耐えられるモデルや2元カソード、3元カソードなど用途に応じてお選びいただけます。
菅製作所のスパッタ装置一覧を見てみる保守管理については、次の項目で説明しましょう。
長期安定性の確保と保守管理のポイント
スパッタ装置を導入した際は、まず当初のプロセス性能の記録を取り、ユーティリティ試験成績表、保守図面を把握しておきましょう。
耐用年数以内でも、偶発的に故障する場合があります。スパッタ装置の多くはディスプレイにエラー表記が出ますので、購入先に問い合わせて修理を依頼することになります。
菅製作所ではアフターケアにも力を入れており、現地に赴き修理を行なったり、簡単な故障かつ急ぎであればWeb上でモニターしながら手順をお伝えして修理していただくなど柔軟に対応させていただいております。
スパッタ成膜と新技術の関連性
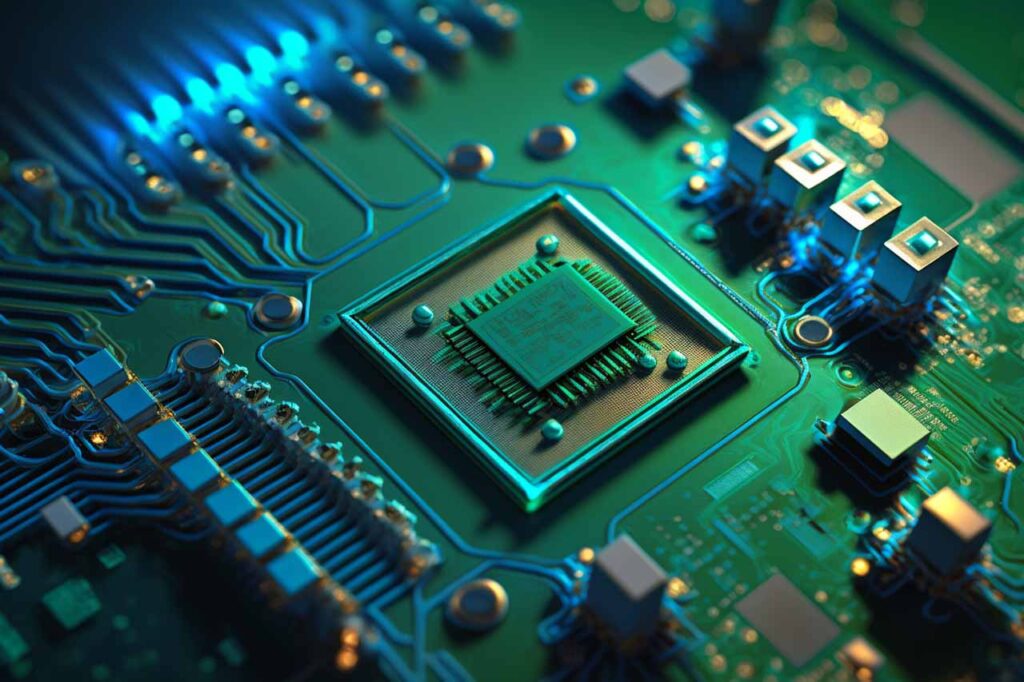
スパッタ成膜がどのようなものに使われているのか、具体的なイメージを見ていきましょう。
半導体の製造プロセス
スパッタ成膜は半導体製造プロセスで広く使用されます。
半導体は金属膜や絶縁体膜を形成する必要があり、半導体そのものが小型化していることからナノスケールでの薄膜が求められます。
スパッタ成膜であれば、ナノスケールで必要な基板に均一の膜を作成できるため、半導体分野では必要不可欠の技術です。
光学部品のコーティング
スパッタ成膜はレンズやミラーなどの光学部品にコーティングする際も役立ちます。
このコーティングによって、光の反射率や透過率の調整ができたり、耐摩耗性が向上したりと様々な恩恵を受けられるのです。
ディスプレイの製造プロセス
高品質なディスプレイの製造プロセスにも、スパッタ成膜は利用されます。
ディスプレイは液晶を透明な電極膜に挟み込んで表示できますが、その透明な電極膜を作成するためにスパッタ成膜が必要となるわけです。
上記のように、目に見えないサイズでありながら私たちの生活で利用されている技術なのです。
装置導入前には菅製作所のテスト成膜サービスをおすすめしています
菅製作所では、導入前にテスト成膜をし、スパッタ成膜の状態を確認していただくサービスを実施しています。
導入するとなると非常に高額なスパッタ装置が必要になりますので、導入に失敗しないためにもぜひ一度テスト成膜をお試しの上、品質がご期待通りであれば導入をご検討いただければと存じます。
テスト成膜ご希望の方は、以下のページよりご連絡ください。
菅製作所にテスト成膜を申し込んでみるまとめ
スパッタ成膜は薄膜を作成する技術の一種で、主に半導体分野で多く使用されます。
仕組みとしては不活性ガスを充満させた真空チャンバー内で、ターゲットに不活性ガスをぶつけ、弾き飛ばされた粒子が基板にコーティングされるという仕組みです。
現代テクノロジーを支える技術の一つですが、装置そのものが高額であり、選び方や保守管理の方法を誤ると損失が大きいという問題もあります。
導入を検討される場合は、製造メーカーとご相談の上、研究や製品製造に十分な効果が得られるスパッタ装置を選びましょう。
菅製作所では、既存の製品についてはもちろん、研究目的に合わせたカスタムも個別に対応させていただきます。テスト成膜サービスも行なっておりますので、スパッタ装置をご検討の際はお気軽にお問い合わせください。
菅製作所に問い合わせてみる