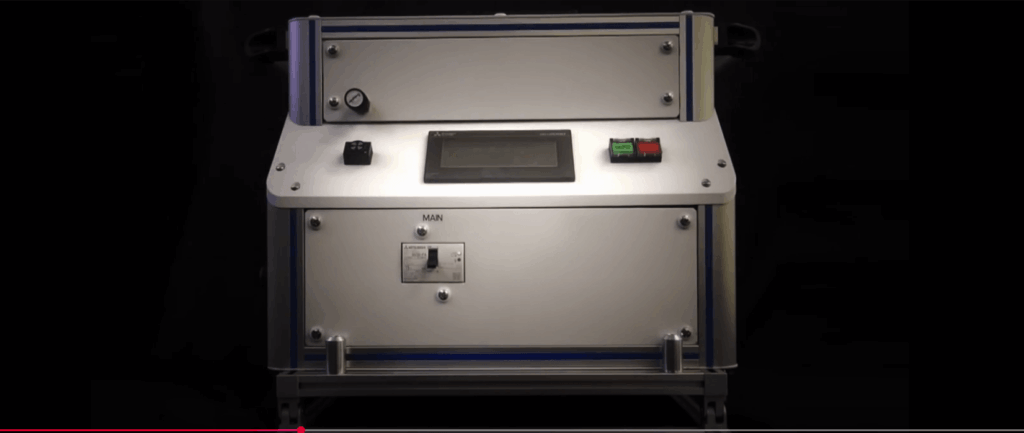
現代の電子機器が小型化・高性能化を遂げる中で、半導体デバイスの微細加工技術はますます重要性を増しています。
その最前線で注目を集めるのが、原子層堆積(ALD)と呼ばれる革新的な薄膜形成技術です。
ALDは、膜を原子1層ずつ積み重ねていくことで、従来の成膜技術では困難だった極めて精密で均一な薄膜を実現します。
本記事では、ALDの基本的な原理から、その優れた特徴、主な種類、そして幅広い応用分野について詳しく解説します。ALD技術の導入をご検討中の方や、最先端の薄膜技術に関心がある方は、ぜひご一読ください。
高精度な薄膜成膜を実現するALD装置をお探しですか?菅製作所は、大学の研究所でも導入実績のあるALD装置で、お客様の研究開発を強力に支援します。個別の研究目的に合わせたカスタマイズや、導入前のテスト成膜も可能です。ALD装置のご検討やご相談は、ぜひ当社までお問い合わせください。
目次
ALD(原子層堆積)とは何か
原子層堆積(ALD:Atomic Layer Deposition)は、ナノスケールで極めて精密な薄膜を形成するための先端的な成膜技術です。
半導体デバイスの高性能化に伴い、より微細な構造が求められる中で、ALDは原子1層ずつ膜を成長させることで、高密度かつ均一な膜を実現し、最先端技術を支える重要な装置として注目されています。
①ALDの原理とプロセス
ALDの核となるのは、自己制限的な表面反応(自己制御)を利用する点です。これにより、膜厚を原子レベルで正確に制御し、優れた膜厚均一性と段差被覆性(ステップカバレッジ)を実現します。
ALDプロセスは通常、以下の4つのステップから成るサイクルを繰り返すことで膜を堆積させます。
例えば、Al(CH3)3(TMA)とO2プラズマまたは水(H2O)を用いたAl2O3(酸化アルミニウム)の成膜では、以下のようになります。
- 第1前駆体導入:
基板に第1の前駆体ガス(例: TMA)を導入します。前駆体は基板表面に吸着し、特定の表面反応を引き起こします。この反応は、表面に利用可能な結合サイトがある限り進行し、サイトが埋まると停止するため「自己制限的」です。余分なTMAは反応せずに排気されます。
- パージ:
導入された余分な第1前駆体ガスおよび反応によって生成された副生成物(例: メタンCH4)を不活性ガス(例: N2やAr)で排出し、反応チェンバーを清浄にします。
- 第2前駆体導入(反応ガス導入):
第2の前駆体ガス(例: 反応性酸素ラジカルまたは水)を導入します。このガスは、基板表面に吸着した第1前駆体と反応し、1層の膜を形成します。この反応もまた自己制限的であり、表面の配位子の数が制限されるため、必要以上に反応が進むことはありません。
- パージ:
反応で残った余分なガスや副生成物をチャンバーから排出します。
この1サイクルでオングストローム(またはそれ以下)スケールの厚さが堆積され、要求される膜厚を得るためにこのサイクルを必要な回数繰り返します。
この「Layer by layer」方式は、パルス成膜法やデジタル成膜法とも呼ばれます。
②ALDの主な特徴と利点
ALDは、その独自の成膜原理により、他の成膜法では得にくい多くの利点を提供します。
超薄膜の精密な制御 | 数nmの超薄膜を原子レベルで正確に制御して堆積させることが可能です。 |
---|---|
優れた均質性・段差被覆性 | 高アスペクト比の構造や複雑な立体構造物に対しても、形状に沿った均一な成膜(コンフォーマルコーティング)が可能です。スパッタリングや従来のCVDでは困難な、狭い細孔の内壁などにも緻密な膜を形成できます。 |
低ピンホール・低パーティクル: | 自己制限的な表面反応により、ピンホールや異物が非常に少ない高品質な成膜が可能です。 |
低ダメージ・低温プロセス | ダメージが少なく、低温での成膜プロセスが実現できます。特にプラズマALDでは低温化が進みます。 |
高い密着性 | 成膜対象物と共有結合を作るため、基板への密着性が高いです。 |
再現性の高いプロセス | 膜厚を厳密にコントロールでき、再現性が高いです。 |
幅広い材料への対応 | 様々な材料の薄膜形成に対応可能です。 |
③ALDの種類
ALDには主に以下の2種類があります。
- サーマルALD(熱ALD):
熱エネルギーを利用して表面反応を促進するALDです。複雑な構造へのコンフォーマルコーティングに適しています。
- プラズマALD(PE-ALD):
プラズマを活用することで、より低温でのプロセスや、前駆体化学の選択肢の拡大、膜質の向上(低抵抗、高密度など)、不純物除去の改善、核生成遅延の減少などが可能になります。リモートプラズマ源を用いることで、プラズマダメージを低く抑えることができます。
④対応可能な材料
菅製作所のALD装置で社内実績があるのは下記の4種です。
酸化物:Al2O3、HfO2、SiO2、TiO2
ALD Windowについて
ALDの自己制御性が成立するプロセスパラメーターの最適範囲を「ALD Window(窓)」と呼びます。この範囲を外れると、自己制御性が失われたり、膜成長が阻害されたりします。ALD Windowは、前駆体、反応ガス、プラズマ源、基板温度、真空装置の排気性能など、様々な条件によって変化します。
他の成膜法との比較
成膜には、ALDの他に化学気相成長(CVD)法やスパッタリング法などがあります。
ALD、CVD、スパッタリングの違い
成膜には、スパッタリングやCVD(化学的気相法)など多彩な装置・手法があります。同じ物質を成膜にする上でも、手法によって特性が変わる場合もあります。以下に、よく比較される3つの方法を整理しました。
化学気相成長(CVD)法 | 成膜したい元素を含む気体を基板表面に送り、化学反応、分解を通して成膜する方法。CVDの中にも基板を加熱させる熱CVD、反応管内を減圧し、プラズマを発生させるプラズマCVDなどの種類がある。 |
---|---|
スパッタリング法 | 放電によるプラズマ中にできたイオン(通常Ar+イオン)を成膜材料の板(ターゲット)にぶつけて材料をはね飛ばします。はね飛ばされた成膜材料が基板へ飛んでいき薄膜を形成する手法です。スパッタリング法では、高融点金属や合金など、蒸着法では困難な材料でも、成膜が可能で、広範囲な成膜材料に対応できます。 |
原子層堆積(ALD)法 | CVDの1種と言われますが、2種類以上の原料気体(プリカーサー,前駆体)を交互に導入・排気を繰り返し,成膜表面に吸着した原料分子を反応させて膜化する方法を原子層堆積(ALD)といいます。 |
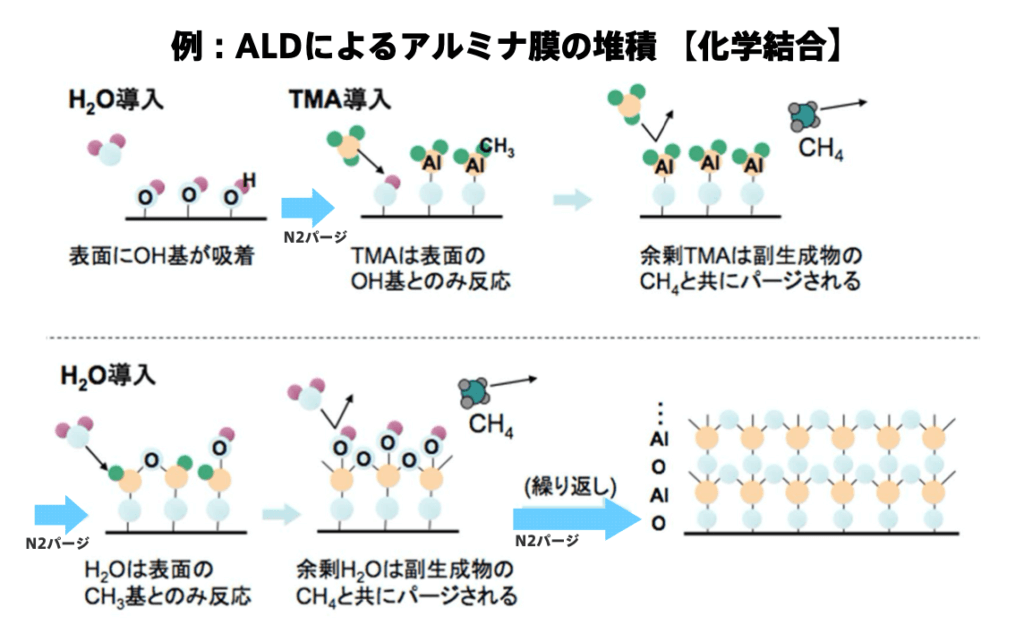
ALDは、原子1層ごとの精密な堆積制御により、CVDやスパッタリングでは難しい高精度かつ均一な薄膜形成が可能です。特に、複雑な3D構造や高アスペクト比の微細構造へのコンフォーマルコーティングにおいて優位性があります。
ALDの応用と装置
ALD技術は、半導体デバイス、ディスプレイ、太陽電池、MEMS/NEMS、2D材料、量子コンピューターデバイス、GaNパワー半導体、ペロブスカイト太陽電池など、多岐にわたる分野での応用が期待されており、今後もその重要性は高まるとされています。
▶菅製作所のALD装置
大学の研究所でも導入実績のあるALD装置をご紹介します。弊社では部品が壊れたらすぐに対応するのはもちろんのこと、研究開発の目的に応じて装置をカスタマイズすることも可能です。お気軽にご相談ください。
SAL1000
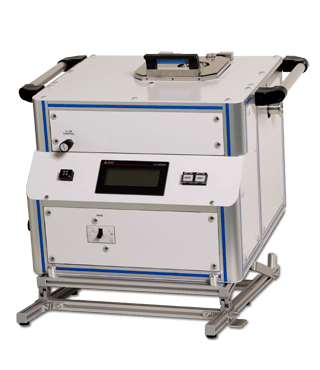
ALD装置のエントリーモデルです。手軽に1原子層ずつの薄膜をつくれます。
【POINT】
- 使いやすさを重視した小型のALD
- 1種類の膜種を成膜する最低限の構成仕様
- デモ機によるテスト成膜が可能
【本体寸法】
W450mm×D450mm×H410mm
プリカーサ | 2個 |
---|---|
膜厚分布 | ≦±3% |
基板加熱 | 350℃ |
複合化 | × |
SAL1000は研究開発用のALD装置(原子層堆積装置)です。
ALD装置は1原子層毎の精密な堆積制御を実現し、均一で凹凸部に対しても段差被覆性に優れた薄膜成形成を可能にする原子層堆積装置(ALD=Atomic Layer Deposition)です。
前駆体と呼ばれるプリカーサボトルに入れた原料を成膜材料として、水やオゾンとの表面化学反応により酸化膜(AL2O3、HfO2、SiO2、TiO2)の成膜をすることができます。
SAL1000はプリカーサを2系統搭載し、1種類の膜種の成膜に必要な基本機能を備えたエントリーモデルのデスクトップ型ALDです。
※例に挙げている膜種に関しては、弊社では実証できていないものが含まれております。
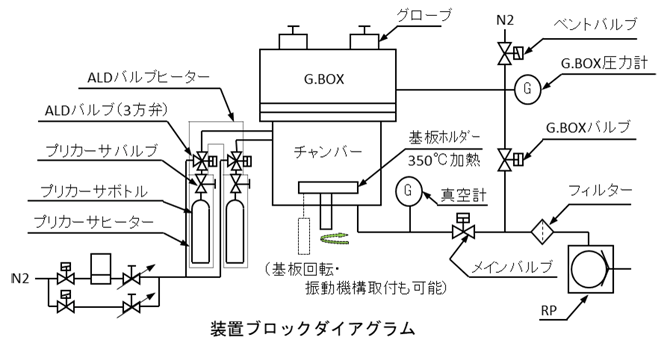
▶PDFカタログ・お問い合わせはこちらから
SAL1000B
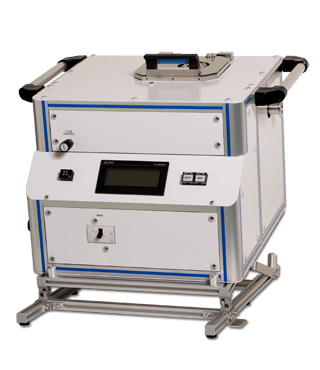
粉体への全周囲成膜を可能にしたALD。卓上型の研究開発用成膜装置です。
【POINT】
- 傾斜+回転+振動で粉体へ成膜可能
- 傾斜角度は水平から45°まで調節可能
- 実は4インチの基板も成膜もできる
【本体寸法】
W582mm×D450mm×H410mm
プリカーサ | 2個 |
---|---|
膜厚分布 | ≦±3% |
基板加熱 | 350℃ |
複合化 | × |
研究開発用の粉体成膜に特化したALD装置(原子層堆積装置)です。
ALD装置は1原子層毎の精密な堆積制御を実現し、均一で凹凸部に対しても段差被覆性に優れた薄膜成形成を可能にする原子層堆積装置(ALD=Atomic Layer Deposition)です。
前駆体と呼ばれるプリカーサボトルに入れた原料を成膜材料として、水やオゾンとの表面化学反応により酸化膜(AL2O3、HfO2、SiO2、TiO2)の成膜をすることができます。
SAL1000Bはプリカーサを2系統搭載した、粉体成膜用途のデスクトップ型ALDです。
粉体への全周囲成膜を可能としたことにより、粉体や粒状の材料に関わる分野で新素材の開発などに活躍します。
※例に挙げている膜種に関しては、弊社では実証できていないものが含まれております。
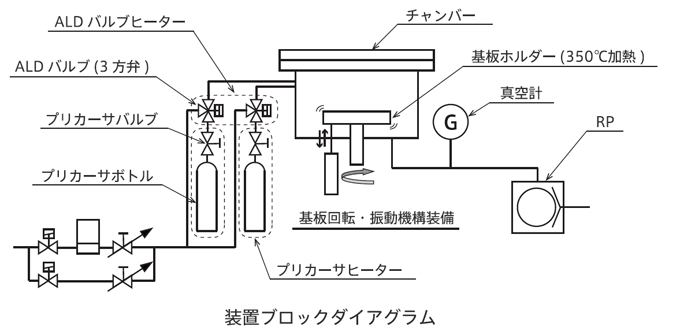
▶PDFカタログ・お問い合わせはこちらから
SAL1000G
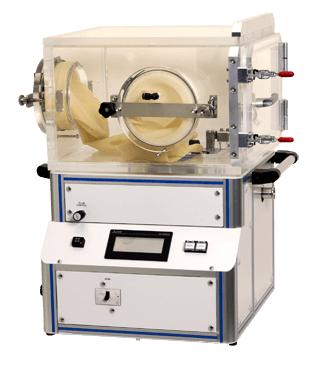
ウエハーまたは粉体への成膜が可能。機能と性能を兼ね備えた卓上型ALDです。
【POINT】
- 真空置換対応のグローブボックス搭載
- 嫌気性のサンプルや材料に対応
- オプションで粉体への成膜が可能
【本体寸法】
W690mm×D590mm×H760mm
プリカーサ | 2個 |
---|---|
膜厚分布 | ≦±3% |
基板加熱 | 350℃ |
複合化 | × |
研究開発用の卓上型ALD装置(原子層堆積装置)です。
ALD装置は1原子層毎の精密な堆積制御を実現し、均一で凹凸部に対しても段差被覆性に優れた薄膜成形成を可能にする原子層堆積装置(ALD=Atomic Layer Deposition)です。
前駆体と呼ばれるプリカーサボトルに入れた原料を成膜材料として、水やオゾンとの表面化学反応により酸化膜(AL2O3、HfO2、SiO2、TiO2)の成膜をすることができます。
SAL1000Gは、卓上型ALDにグローブボックスを装備し、酸化や大気と反応する嫌気性の材料を用いた成膜ニーズに対応するモデルです。
また、オプションの粉体成膜用振動機構及び傾斜フレームを装備することで、粉体への全周囲成膜も可能としました。
※例に挙げている膜種に関しては、弊社では実証できていないものが含まれております。
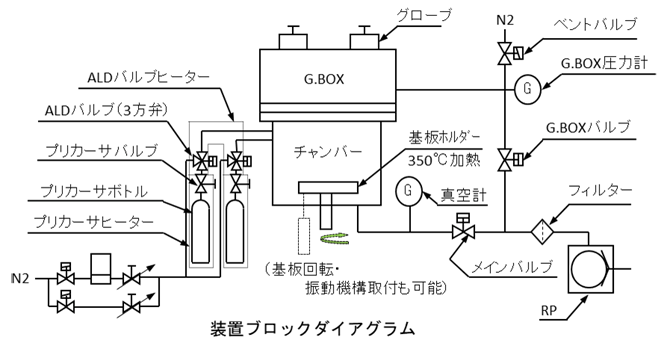
▶PDFカタログ・お問い合わせはこちらから
SAL1100
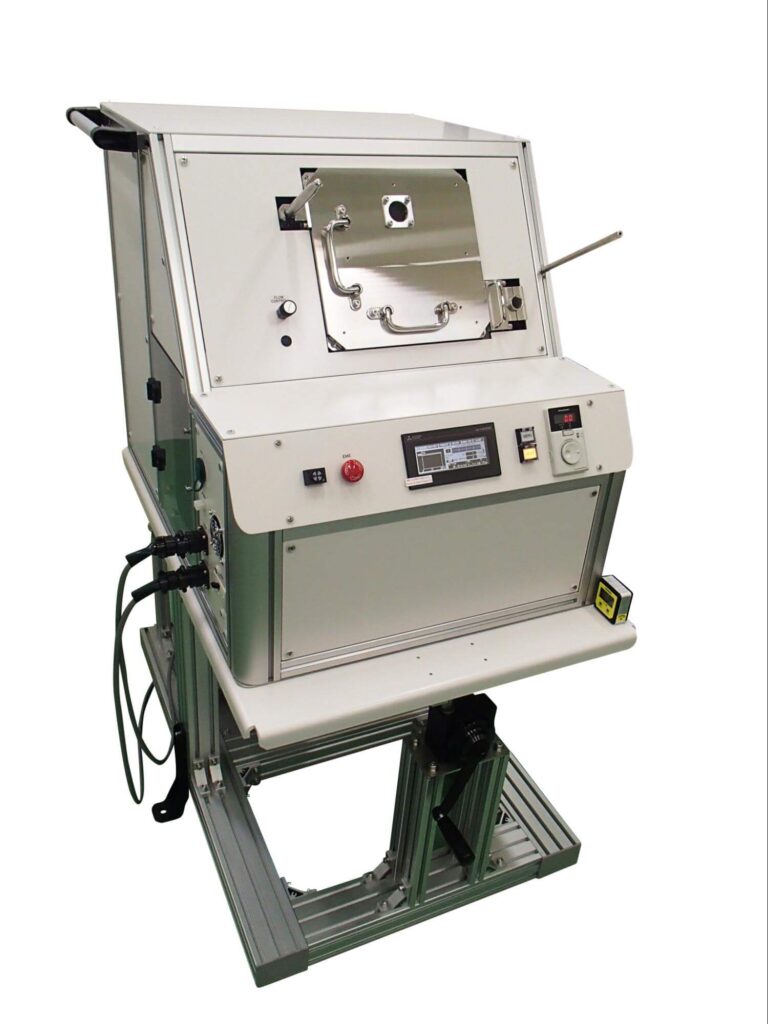
従来モデルSAL1000Bの最大5ccから32倍に容量UP!1バッチ160ccのペレットや粉体に成膜可能。ドラム型の研究開発用ALD成膜装置です。
【POINT】
- 斜め回転ドラム式アルミ製試料ホルダーを装備、ペレットや粉体を攪拌しながら成膜
- 試料ホルダーは最大50rpmまで回転数を可変可能
- 成膜レシピの記憶/読み込みが可能
【本体寸法】
W1000mm×D1000mm×H1500mm(メンテナンスエリア含む)
プリカーサ | 2個 |
---|---|
膜厚分布 | 規定なし |
基板加熱 | Max400℃ |
複合化 | × |
研究開発用の粉体成膜に特化したALD装置(原子層堆積装置)です。
ALD装置は1原子層毎の精密な堆積制御を実現し、均一で凹凸部に対しても段差被覆性に優れた薄膜成形成を可能にする原子層堆積装置(ALD=Atomic Layer Deposition)です。
前駆体と呼ばれるプリカーサボトルに入れた原料を成膜材料として、水やオゾンとの表面化学反応により酸化膜(AL2O3、HfO2、SiO2、TiO2)の成膜をすることができます。
SAL1100はプリカーサを2系統搭載した、粉体成膜用途のドラム型ALDです。
粉体への全周囲成膜を可能としたことにより、粉体や粒状の材料に関わる分野で新素材の開発などに活躍します。
※例に挙げている膜種に関しては、弊社では実証できていないものが含まれております。
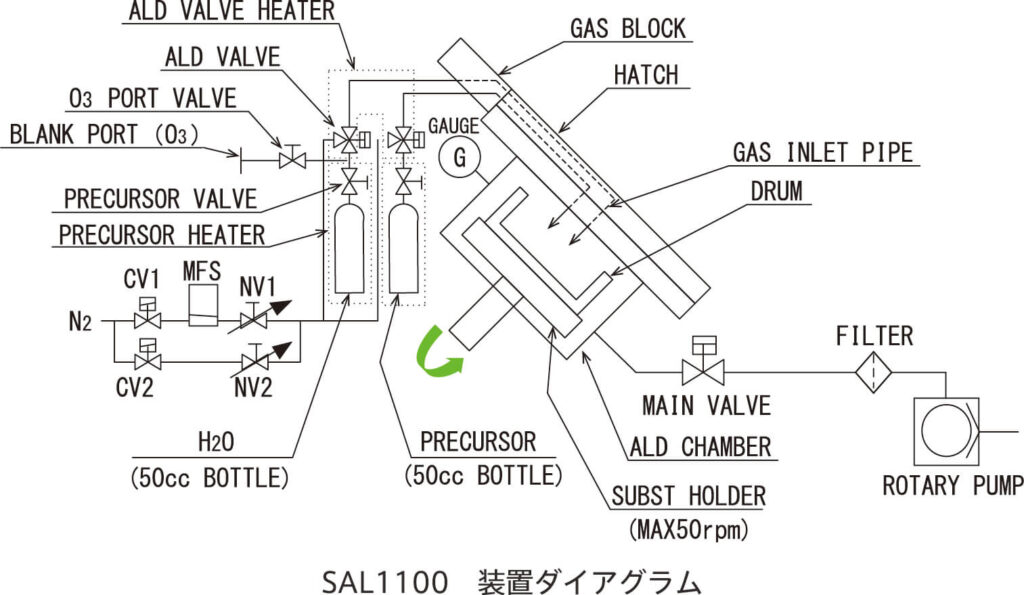
▶PDFカタログ・お問い合わせはこちらから
SAL3000
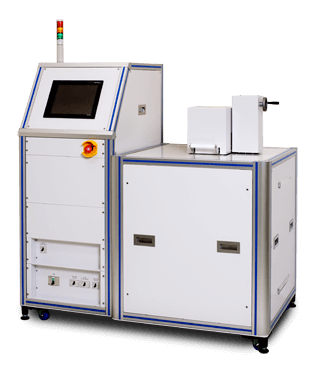
小型で機能充実のALDです。
【POINT】
- SAL3000標準型から横幅が4割小型化
- 成膜方向はデポアップかダウンを選択
- デモ機によるテスト成膜が可能
【本体寸法】
W835mm×D700mm×H1644mm
プリカーサ | 4個(最大6個) |
---|---|
膜厚分布 | ≦±3% |
基板加熱 | 350℃(800℃) |
複合化 | × |
研究開発用のALD装置(原子層堆積装置)です。
ALD装置は1原子層毎の精密な堆積制御を実現し、均一で凹凸部に対しても段差被覆性に優れた薄膜成形成を可能にする原子層堆積装置(ALD=Atomic Layer Deposition)です。
前駆体と呼ばれるプリカーサボトルに入れた原料を成膜材料として、水やオゾンとの表面化学反応により酸化膜(AL2O3、HfO2、SiO2、TiO2)の成膜をすることができます。
SAL3000は従来からあるデポダウン方式の仕様に加え、基板へのパーティクル付着をより低減できる「デポアップ」タイプをご用意しております。更に目的に合わせ自動基板搬送用ロードロック室や真空置換グローブボックスを選択できるようになっています。
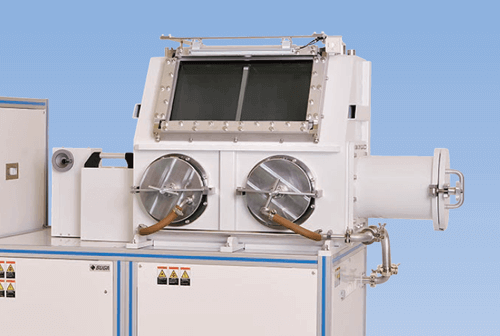
※例に挙げている膜種に関しては、弊社では実証できていないものが含まれております。
▶PDFカタログ・お問い合わせはこちらから
SAL3000Plus
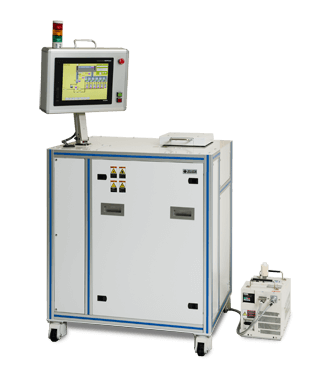
小型で機能充実のALD。他装置との複合化で幅広い実験に対応可能です。
【POINT】
- SAL3000標準型から横幅が4割小型化
- 成膜方向がデポアップとダウンから選択
- Plusシリーズの別装置と連結可能
【本体寸法】
W835mm×D700mm×H1644mm
プリカーサ | 4個(最大6個) |
---|---|
膜厚分布 | ≦±3% |
基板加熱 | 350℃(800℃) |
複合化 | 〇(SAL3000+U) |
研究開発用のALD装置(原子層堆積装置)です。
ALD装置は1原子層毎の精密な堆積制御を実現し、均一で凹凸部に対しても段差被覆性に優れた薄膜成形成を可能にする原子層堆積装置(ALD=Atomic Layer Deposition)です。
前駆体と呼ばれるプリカーサボトルに入れた原料を成膜材料として、水やオゾンとの表面化学反応により酸化膜(AL2O3、HfO2、SiO2、TiO2)の成膜をすることができます。
SAL3000PlusはSAL3000の成膜性能を維持したまま本体の大幅な小型化に成功し、加えて他の装置との複合化も実現による幅広い成膜プロセスに対応した高性能ALD装置です。
SAL3000Plusは、本体側面に拡張用ポートを備えており、トランスファーユニットSTR2000と連結することで、ロードロック機能が備わります。
Plusシリーズのスパッタ装置、アニール装置、蒸着装置、そして同じALDのSAL3000Plusと複合化が可能で、基板を大気に曝さず多様な成膜プロセスが可能です(※複合化で組み合わせる装置によっては、接続用のポート位置を左右反転させた構造にする必要があります)。
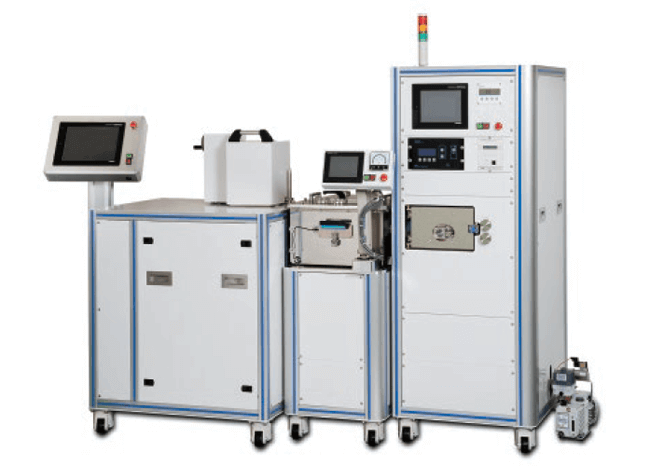
上記はアニール装置との複合化例です。
※例に挙げている膜種に関しては、弊社では実証できていないものが含まれております。
▶PDFカタログ・お問い合わせはこちらから
SAN1000
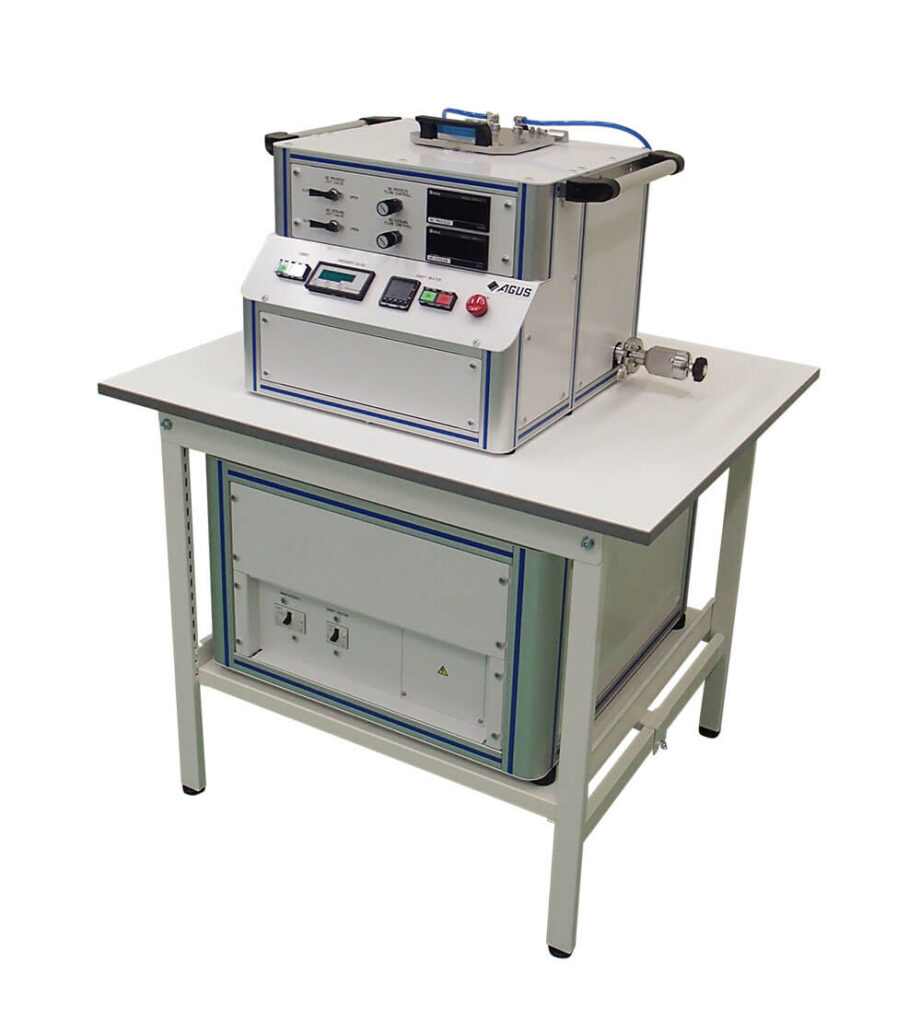
基板への高温加熱処理(アニール)や不活性ガス導入による熱処理時の圧力コントロールが可能です。
【POINT】
- N2またはArガス導入時でも1000℃まで均一・急速加熱
- 基板を吹き飛ばさず急速冷却
- 省スペース配置が可能な小型サイズ
【本体寸法】
W582mm×D450mm×H411mm
プリカーサ | 200℃〜1000℃ |
---|---|
到達圧力 | ≦10Pa |
複合化 | 〇(SAL3000+U) |
SAN1000卓上アニール・窒化処理装置は、4インチまでの基板を赤外線照射により、真空中またはガス雰囲気中のクリーンな環境で加熱処理することができます。
また、卓上設置型ができる小型サイズで、チャンバーに水冷機構、基板にガスフローによる冷却機構を備えており処理後の基板を短時間で取り出すことのできるバッチ式の装置です。
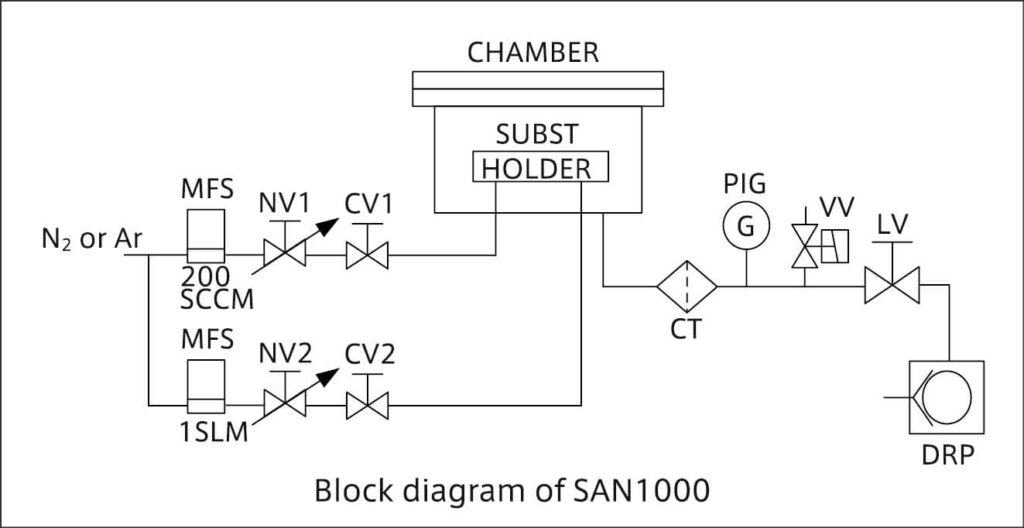
▶PDFカタログ・お問い合わせはこちらから
SAN2000Plus
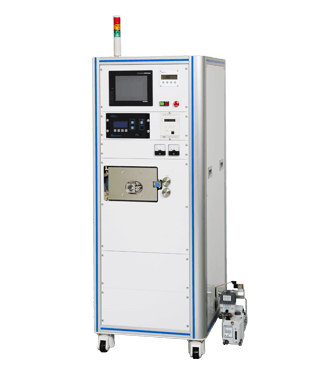
基板への高温加熱処理(アニール)や反応性ガス導入による熱処理が可能です。
【POINT】
- 200℃~1000℃の加熱制御機能を搭載
- RF電源搭載モデルならプラズマ処理が可能
- スパッタやALD装置との複合化に対応
【本体寸法】
W608mm×D460mm×H1827mm
加熱制御温度 | 200℃〜1000℃ |
---|---|
到達圧力 | 10^-5 |
プラズマ処理 | 搭載可 |
複合化 | 〇 |
SAN2000Plus アニール装置は、4インチまでの基板を強力な赤外照射により、真空中または真空ガス雰囲気中のクリーンな環境で加熱処理することができます。
更に、基板表面の有機膜,金属膜の除去、表面改質等が可能なプラズマプロセス技術をシリーズに加え、基板成膜の前工程処理と後工程処理を1台2役として兼用することが可能です。
装置購入後でもフロッグレッグ基板搬送機構を持つ廉価型STR2000トランスファーと接続可能なため、スパッタ装置,蒸着装置等の成膜装置と容易に複合化することができ、将来拡張するご予定のあるお客様に最適なアニール装置です。
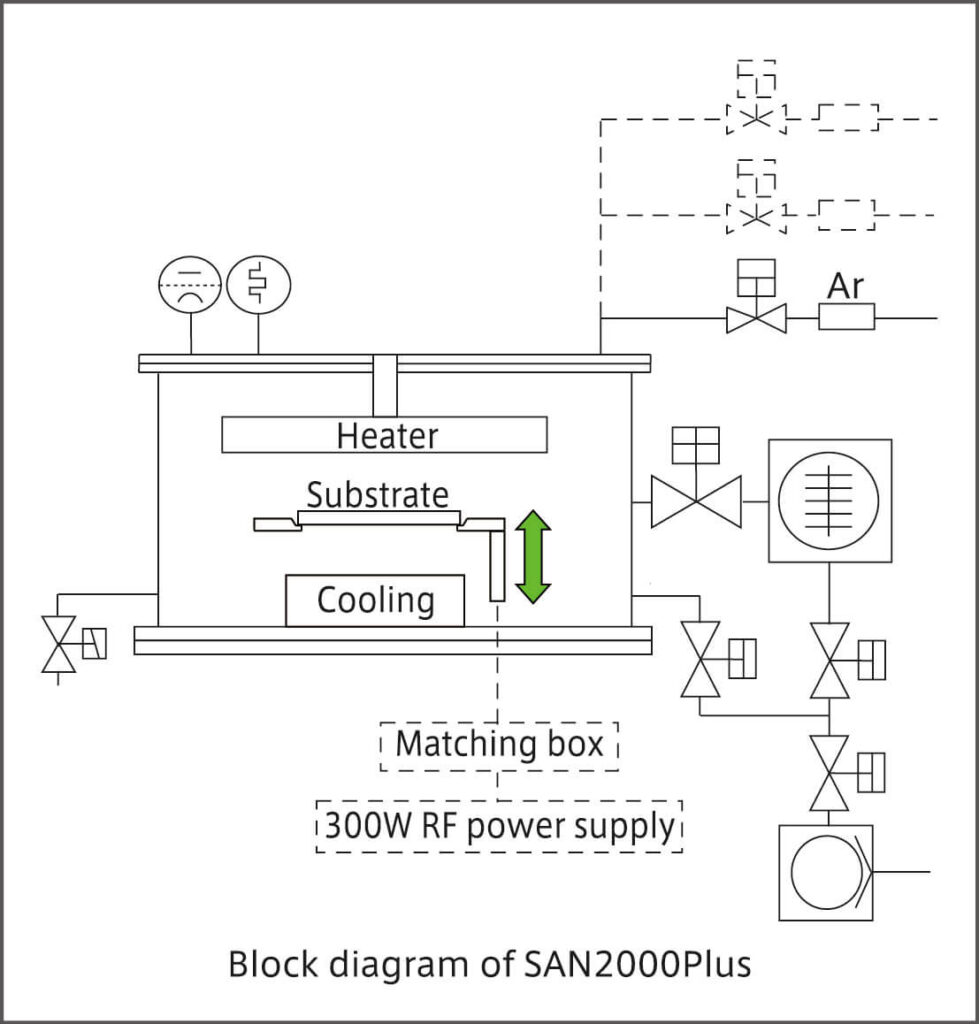
▶PDFカタログ・お問い合わせはこちらから
▶関連動画
【参考】
まとめ
原子層堆積(ALD)は、自己制限的な表面反応を利用し、原子1層ずつ精密に薄膜を形成する画期的な技術です。超薄膜の正確な制御、優れた均質性・段差被覆性、低ダメージプロセスなど、従来のCVDやスパッタリングにはない多くの利点を提供します。
サーマルALDとプラズマALDがあり、酸化物、窒化物、金属など幅広い材料に対応します。半導体、ディスプレイ、太陽電池といった多様な分野でその応用が期待されており、今後も技術革新を牽引するでしょう。適切なALD装置を選定し、その特性を最大限に引き出すことが、高品質な薄膜作製と技術発展の鍵となります。